VSI Crusher Rotor Tips Assembly and Its Removal and Installation
What is the VSI crusher rotor tip assembly?
A VSI (Vertical Shaft Impact) crusher rotor tip assembly is a component in the crushing chamber of a VSI crusher that accelerates rocks or other materials to high speeds, causing them to collide with a stationary surface and break into smaller pieces. The rotor tip assembly is the wear part of the rotor that contacts the material being crushed, and it is usually made of tungsten carbide, a hard and wear-resistant material. The assembly typically consists of a number of individual tips that are attached to the rotor by a screw or bolt. The design and shape of the tips can vary depending on the application and the type of material being crushed. The quality and condition of the rotor tip assembly can have a significant impact on the performance and efficiency of the VSI crusher.
The VSI crusher rotor tip assembly includes:
- Rotor Tips
- Tip/cavity Wear Plates
- Back-up Tips
Rotor Tips
VSI (Vertical Shaft Impact) crusher rotor tips are the outer wear part of the rotor assembly in a vertical shaft impact crusher. The rotor tips are designed to add operational uptime by providing resistance against wear caused by sand, stones, and other abrasive materials that are fed into the crusher.
The VSI crusher rotor tips are typically made from tungsten carbide or other similar materials that are known for their high resistance to wear and abrasion. These materials are designed to withstand the high-speed impact and crushing forces generated by the rotor assembly during operation.
The design of the VSI crusher rotor tips plays an important role in determining the efficiency of the crusher. The shape and size of the rotor tips can affect the velocity and direction of the material being crushed, as well as the amount of material that is being crushed at any given time. As a result, proper maintenance and replacement of the rotor tips is critical to ensuring optimal performance and uptime of the VSI crusher.
Rotor Tips Wear
Rotor tips must be checked to determine the amount of wear on the inserts. Tips need to be replaced once 95% of the insert has been removed at the center of the wear. The back- up tip assembly will protect the rotor body from damage, therefore a tip in this condition could be run for another shift. Experience will help the operator understand the wear performance of the tip. Ensure that the rotor tips are tightly held and not broken, cracked, or badly chipped.
Normal Wear
The rotor tips are wearing normally. Replace when less than 3mm [1 /8 in.] of insert remains at the center of the wear, or if the tip will not last another shift.
Cracked or Chipped Inserts
Tramp iron in feed. Remove the tramp iron. Oversize feed material. Investigate the cause of oversize. Reduce maximum feed size.
Off Centre Wear
The rotor tips are wearing at the top or bottom, not in the center. The trail plate angle may require altering.
Selection of Rotor Tips
A range of rotor tips is available to suit differing feed material characteristics, operating conditions, and types of rotor (i.e. deep, standard). The rotor tips supplied with your machine have been carefully chosen to suit your requirements. However, changing feed material can require the re-selection of the rotor tips.
For information regarding rotor tip options, contact your Qiming Casting representative.
Tip/cavity Wear Plates
Tip/cavity wear plates are a component of a VSI crusher that protect the rotor’s metal tip from wearing down due to the crushing process. These plates are typically made of tungsten carbide, a very hard and wear-resistant material, and are installed at the bottom of the crushing chamber, where the material is fed into the crusher.
The tip/cavity wear plates can be replaced periodically when they become worn down, ensuring the longevity and effectiveness of the VSI crusher. By protecting the rotor’s tip from excessive wear, the tip/cavity wear plates also help maintain the desired shape and size of the crushed material.
Tip/cavity Wear Plates Wear
Initially, the tip/cavity wear plates may wear quickly until they reach a certain profile governed by the application. This is quite normal and should not cause concern.
Tip/cavity wear plates must be inspected for wear and be replaced when there is doubt they will last another shift, or as soon as wear appears on the top of the bolt head. Replace tip/cavity wear plates that have cracked. Check that tip/cavity wear plates are not loose.
Normal Wear
The tip/cavity wear plates are wearing normally. Replace when wear just starts to show on bolt head.
Cracked Tip/Cavity Wear Plates
Caused by tramp iron, oversize feed, excess build-up with damp/sticky material, or uneven mating surface. Remove the tramp iron. Reduce feed size. Ensure that mating surfaces are flat, i.e. there is no spatter or grit between tip/cavity wear plate and back-up tip.
Uneven Wear
Tip/cavity wear plates are wearing at the top or bottom, not in the centre. Adjust trail plate angle. Uneven wear can also be caused by excessive crushing chamber build-up. Premature top wear can be indicative of a worn cavity ring and/or cascade wear skirt. Premature bottom wear can be indicative of excessive build up in the base.
Back-up Tips
VSI crusher backup tips are a type of wear component that is used in vertical shaft impact (VSI) crushers to protect the rotor’s tip from wear and damage. These tips are also known as tungsten carbide tips or VSI crusher tip plates.
The backup tips are typically made from tungsten carbide, a hard and durable material that can withstand the high impact and abrasion forces that are generated during the crushing process. They are designed to be easily replaceable, which helps to extend the life of the rotor and reduce downtime for maintenance.
The VSI crusher backup tips are positioned on the rotor’s top and bottom edges and are secured with screws. The tips are designed to be flipped or replaced when they become worn or damaged, allowing the rotor to maintain its balance and crushing efficiency.
Back-up Tips Wear
In normal operation, the back-up tip should be unused and in many cases is not visible (depending on rotor tip and tip/cavity wear plate style used).
Normal Wear
The back-up tip is only exposed to wear when the rotor tip has failed or worn out. In the event of emergency use of the back-up tips, they should be replaced once there is only 3-5 mm [1 /8 – 3/16 in.] of insert remaining at the centre of the wear path. Back-up tips should also be replaced if the insert is cracked or badly chipped.
Irregular Wear
Rotor tips are being left in place too long and wearing out.
Back-up Tips Breaking
Rotor tip failed, exposing back-up tip, usually caused by tramp iron or oversize feed or having been worn too thin.
Rotor Tip Assembly Removal and Installation
Removal
Remove taper bolts. Tap the rotor tip inward to break away build-up that will hold tip and back-up tip in place. It may be necessary to use a bar to chisel away very tightly compacted build-up. If this condition persists it is advisable to wash out build-up with water.
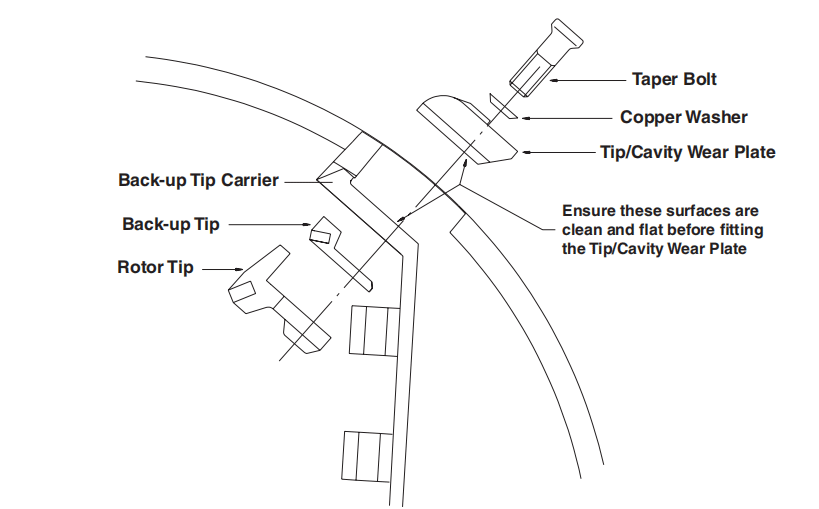
Rotor Tip Assembly Removal
Installation
Ensure that all mating surfaces on the rotor tip, tip/cavity wear plates, and back-up tips are free of any high spots (dirt, weld spatter, burrs). Position back-up tip, rotor tip, and tip/cavity wear plate in the rotor port. Insert taper bolts, ensure that the copper washer is in place, and tighten. (Applying anti-lock compound to the thread will make removal easier). Ensure that the tip assembly is pulled up tight and that there is no movement in the parts.