High-Quality Crusher Jaw Plates For Popular Brands
Qiming Casting is one of the leading suppliers of durable wear solutions, supplying over 30 years of high-grade, high-quality crusher jaw plates for popular brands. Our diverse teams have engineered the finest jaw plates, innovatively designed to withhold high impact and abrasion.
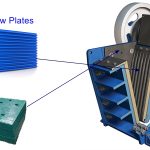
Crusher Jaw Plates
What is Crusher Jaw Plates?
A crusher jaw plate protects and supports the jaw crusher. A jaw plate is the most frequently changed wear part, so ensuring a quality graded jaw crusher is crucial. Jaw plates, also called ‘jaw dies, ‘ are often made of a mixture of graded composite or high-resistance steel.
Working Principles
Usually, in a conventional crushing operation, there are two jaw plates of moveable and stationary jaws. These jaws are located on the opposite sides of the crushing chambers. To fully segment and fracture the material, the moveable jaw plate works reciprocally to press the material against the fixed plate. The material continues to be crushed on the fixed jaw until refined enough to get through the jaw gap.
Durable Crusher Jaw Plates by Qiming Casting
Our team of experts has specially engineered our high-strength and resistant crusher jaw plate liners for a seamless crushing experience. Our double wear resistance technology makes our crusher jaw plates much more efficient than ordinary high manganese steel liners.
With over 30 years of proven record of being one of the best mining tools suppliers worldwide, Qiming Casting offers innovative mining solutions customized to the very detail to best suit your machinery profile.
Our Premium Crusher Jaw Plates features;
- High Impact strength, durability, and resistance
- Customized in every detail with maximum prevention and easy replacement
- 100% prevention of erosion, increasing crushing uptime and wear life
- Longer wear life leads to reduced maintenance time and cost