Premium Crusher Blow Bars For Popular Brands
Qiming Casting is one of the leading suppliers of durable wear solutions, supplying over 30 years of high-grade, high-quality chrome steel and Metal Matrix Composite blow bars for all kinds of popular brands. Our diverse teams have engineered the finest blow bars, innovatively designed to withhold high impact and abrasion.
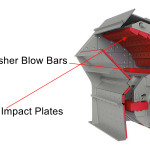
Crusher Blow Bars
What are Crusher Blow Bars?
Crusher blow bars, or ‘impact blow bars,’ are crucial wear items for impact crushers. A blow bar diverts the material towards the crushing chamber. The material fractures into smaller segments as soon as it comes in contact with the impact wall. They ensure the machine is appropriately undergoing the crushing process. Crusher blow bars must be replaced in time to avoid damage to other integral parts of the machinery.
Working Principles
A crusher blow bar is used in horizontal shaft crushers and is mounted on top of the rotor, stacked in groups of 3 or 4 pieces. Once the machine starts, the material comes in contact with the bar and is immediately crushed. A crusher blow bar is made up of high-resistance steel with various other materials that can be customized in accordance with machinery specifics and the client’s needs. A crusher must first be made in light of what will accurately match your machinery’s profile, which is what we do here at Qiming Casting.
Durable Crusher Blow Bars by Qiming Casting
Qiming Casting is one of the leading front players in the mining industry, distributing quality mining goods for over 30 years. We offer specific customized shapes and metallurgical material specifications to match diverse operating processes and crushers. Our consistent quality has made us one of the biggest suppliers of high chrome blow bars in the Middle East and Spain.
We offer a range of engineered crusher blow bars tailored to the details of your machinery profile. Our team conducts a thorough specification test on your machine to create customized blow bars.
It’s important to note the material used in your crusher blowbars. The composition of materials determines whether the blow bar would be an adequate fit against the abrasive material.
Every delivered blow bar is made of high-strength, wear-resistant material. Some of our most independent materials currently on the market are;
- Manganese steel
- Chrome steel
- Martensitic steel
- Chrome + Ceramic
- Martensitic + Ceramic