Why use TIC inserts manganese hammer?
The shredder hammer is mostly made of high manganese steel, which is a kind of anti-wear material with a long history. In recent 10 years, domestic and foreign scientists have studied high manganese steel from many aspects in order to further improve its wear resistance:
- Some foundries add Mo, Ni, and other rare elements to improve the wear resistance;
- Some foundries add Cr element to increase the hardness of the hammer;
- Some foundries change the ratio of manganese to carbon to improve the wear resistance;
- Some factories improve the service performance of high manganese steel by pre-surface hardening treatment and improving smelting, casting, and heat treatment processes.
The research of these scholars has achieved certain results in improving the wear resistance of high manganese steel, but for some conditions with large impact force and larger parts, such as some big shredder hammers, it is still not ideal to use high manganese steel.
In order to solve this problem,Qiming Casting uses TIC rods inserts manganese body to increase the working life.
TIC inserts manganese hammer experimental methods
For this new material, we choose manganese steel as the matrix material. The chemical composition as the following:
- C 1.1-1.2%
- Mn 12.5-13.2%
- Si 0.5-0.6%
- P 0.04-0.05%
- S 0.009-0.02%
For the TIC rods, we choose a 20mm*20mm*40mm cuboid:
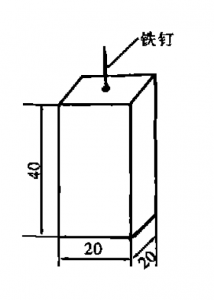
TIC cuboids
We use the sand casting method to cast a 120mm*120mm*120mm sample product. The samples were heat-treated in a box-type resistance furnace with water toughening treatment at 1050 ℃. The interface was observed by the naked eye, and then the microstructure, structure, and element distribution near the interface were analyzed by optical microscope and electron probe microanalysis (JCXA-733).
Experimental results and discussion
After machining, the surface of the sample was observed by naked eyes. It was found that there was no gap at the junction of high manganese steel and TIC cuboid except for different colors (high manganese steel was white, IC cuboid was black), which indicated that the two materials were well combined.
The hardness of the TIC cuboid before casting is HRC 59-61. After casting with high manganese steel and water toughening treatment, the hardness of the sample surface is tested. The results show that the hardness of the middle region of TIC cuboid remains unchanged (HRC60), but the hardness of the region near the cemented carbide and high manganese steel decreases to hrc58, Moreover, the hardness of high manganese steel near the TIC cuboid (HRC: 30-60) is much higher than that far away from the TIC cuboid (HRC: 22-24), which indicates that there is a transition zone between the hardness of the two materials at the junction of high manganese steel and TIC cuboid, which is due to the mutual penetration of high manganese steel and TIC cuboid.
In order to better check the bonding condition of the interface between the two materials, the metallographic samples were cut at the cast-in joint, and the microstructure near the interface was analyzed by electron probe after polishing. The SEM photograph of the joint is shown in Fig. 3. It can be seen from the picture that the matrix of cemented carbide is well combined with high manganese steel, but the joint is not seen, that is, the high manganese steel and cemented carbide matrix are fused into one. On one side of high manganese steel, the area with TiC particles sparsely distributed can be seen. That is to say, the hard phase tic in cemented carbide partially drifts from one side of cemented carbide to the other side of high manganese steel. This is because the high manganese steel melts the surface matrix of cemented carbide in the process of casting, which makes the hard phase tic on the surface drift to the high manganese steel. After cooling and solidification, these TiC particles are randomly fixed in the high manganese steel.

Fig. 3 SEM image at the bond of two materials
In order to better explain the bonding condition of the two materials’ interface, the distribution of Ti element in a field of view is made at the joint. Figure 3 shows the surface distribution of SEM image and Ti elements in the same field of view. It can be seen from Figure 4 that the characteristic X-ray images of Ti elements are enriched on the cemented carbide side, and the characteristic X-ray images of Ti elements are also found near the interface area on the side of high manganese steel. It is shown that Ti elements exist on the side of high manganese steel 1, which is due to the metallurgical combination of two materials during casting, and the tic in the cemented carbide drifts to the high manganese steel side, and during heat treatment, The Ti element in tic diffuses to high manganese steel. It can be seen that TiC particles are very firmly combined with high manganese steel.
The experimental results show that the combination of TIC cuboid and high manganese steel is metallurgical. There is a transition zone in the interface of the two kinds of materials, no matter in hardness, or in the distribution of microstructure, structure, and elements, which makes the cemented carbide cast firmly in the high manganese steel. In the process of use, high hardness cemented carbide plays a role in resisting material wear, thus greatly improving the service life of the material.

Fig. 4 SEM image at the bond of two materials and distribution of Ti
TIC inserts manganese hammer usage
In order to investigate the service performance of inlaid cast high manganese steel, several cylindrical cemented carbides were inlaid on the easily worn surface of the hammer (as shown in Figure 5, mass 120 kg). Before casting, the cemented carbide (~ 25 mm × 40 mm) should be polished with emery cloth, one iron nail should be welded on one end of each cemented carbide, and the other end of the iron nail should be inserted into the sand mold, so as to fix the cemented carbide in the mold cavity. After pouring, cemented carbide is inlaid in high manganese steel.
The hammerhead made by the above method is used in the Hongyun quarry in Shunde, Guangdong Province. The broken materials in the quarry are hard stones used in expressways, and their service life is 20 days. The service life of the original high manganese steel hammer is only 7 days, and the cost of the cast in hammer is only 30% higher than that of the high manganese steel hammer, which shows the good economic and social benefits of the cast in the hammer.
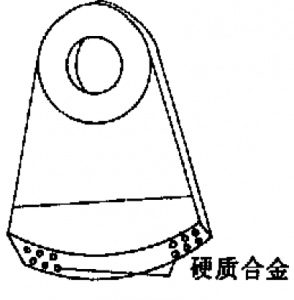
Fig. 5 TIC inserts hammer
The results
Based on Qiming Casting’s experimental results, Our TIC inserts manganese hammer span life longer than other material. This new design hammer not only suits hammer mill wear parts but also suits shredder wear parts. If you any question about this new material, please contact us freely!
[wpforms id=”3777″]