90kg Manganese Steel Hammer Research And Application
Over the years, in the building materials, metallurgy, mining, power industry, large hammer crusher hammers are made of ordinary high manganese steel, hammer weight is less than 70 kg. In use, it has low wear resistance and is easy to break, causing equipment damage accidents from time to time. With the rapid development of China’s modern industry, cement production lines with a daily output of 2000-4000 tons have been launched one after another. At the end of the 1980s, China has successively imported large Hammer Crushers from Germany, Denmark, and other countries. The hammers with a supporting capacity of more than 90 kg have to be imported from abroad due to the lack of successful production experience in China.
Large hammer crusher equipped with more than 90 kg hammer weight, high-speed cyclic impact force, the working conditions are very bad, and ordinary high manganese steel can not provide both any fracture and good wear resistance. In this case, we investigated the hammers imported from Germany and Denmark by Jidong, Zhujiang, and other cement plants, and combined with the characteristics of China’s resources, developed a 90 kg grade super high manganese steel hammer.
Manganese Steel Hammer Chemical Composition Design
Based on the 90kg manganese steel hammer working conditions, the hammer must have high impact toughness, good wear resistance, and fracture resistance. At the same time, according to its own weight and large section thickness, the following composition design is carried out.
- Carbon (C): carbon is the dominant element in steel which affects various properties. In order to make the steel have high strength, hardness, good wear resistance, and enough toughness to ensure no fracture in use, w (c) = 0.95% ~ 1.25%.
- Manganese (Mn): higher manganese carbon ratio is to obtain austenite structure after water toughening treatment. When manganese is continuously increased on the basis of W (MN) = 13%, although the strength and toughness of the steel are not much improved, it can reduce the precipitation of carbides in the structure of thick and large section, which has a great effect on improving the toughness. Therefore, adding the appropriate amount of chromium into the steel at the same time, the increase of manganese content can also reduce the harmful effect of chromium on promoting carbide precipitation in a cast state. Therefore, the manganese content in the steel is increased to 17% ~ 20%.
- Silicon (Si): Silicon is a conventional content, which has a significant solid solution strengthening effect. Adding 0.40% ~ 0.80% silicon is to deoxidize and improve the casting process performance. If the silicon content is further increased, the toughness of the steel will deteriorate.
- Chromium (Cr): adding 2.0% ~ 3.0% chromium is to improve the yield strength and wear resistance of the steel. If the content of chromium is too high, the toughness of the steel will be reduced and the properties will deteriorate.
- Molybdenum (Mo): the existence of a small amount of carbide in the steel is beneficial to improve wear resistance and yield strength. The purpose of adding 0.20% ~ 0.50% molybdenum is to improve the distribution and morphology of carbide in the steel and improve the microstructure and properties of the steel.
- Phosphorus and sulfur (P, S): harmful elements in steel, reduce the mechanical properties of materials, increase the cracking tendency of castings in casting and heat treatment, and do great harm to steel. Therefore, w (P) ≤ 0.07%, w (s) ≤ 0.05% should be strictly controlled.
So the chemical composition of this hammers in the following:
- C 0.95% ~1.25%
- Mn 17% ~20%
- Cr 2% ~3%
- Mo 0.2% ~0.5%
- Si 0.4% ~0.8%
- P ≤ 0.07%
- S ≤ 0.05%
Effect of heat treatment process on mechanical properties and microstructure
Table 2 Test results of the heat treatment process | ||||||
Quenching temperature | 1 050 ℃ | 1100 ℃ | 1150 ℃ | |||
Sample value | Average value | Sample value | Average value | Sample value | Average value | |
Tensile strength | 640 | 679 | 851 | 813 | 648 | 726 |
772 | 832 | 865 | ||||
625 | 755 | 665 | ||||
Impact toughness | 39 | 65 | 166 | 176 | 122 | 116 |
46 | 175 | 93 | ||||
110 | 187 | 132 | ||||
Hardness (HB) | 241 | 240 | 240 | 238 | 213 | 210 |
252 | 245 | 211 | ||||
227 | 230 | 205 | ||||
Metallographic structure | Austenite + carbide (grade 4a) | Austenite + carbide (grade 4a-3a) | Austenite + carbide (grade 3a) | Austenite + carbide (grade 3a) | Austenite + carbide (grade 3a) | Austenite + carbide (grade 4a-3a) |
Austenite + carbide (grade 4a) | Austenite + carbide (grade 3a) | Austenite + carbide (grade 4a) | ||||
Austenite + carbide (grade 3a) | Austenite + carbide (grade 3a) | Austenite + carbide (grade 4a) |
We made three groups of experimental samples for three different temperatures of heat treatment to compare:
- The carbide of manganese steel hammer after water toughening treatment at 1050 ℃ dissolves less into austenite, resulting in high hardness, low impact toughness, and tensile strength, which will cause the hammer to fracture due to insufficient toughness and low strength;
- After 1150 ℃ water toughening treatment, the amount of carbides dissolved into austenite is more due to the high quenching temperature, resulting in low hardness, which will reduce the wear resistance and shorten the service life;
- The strength and impact toughness of manganese steel treated at 1100 ℃ are better than those of the other two groups, with higher hardness and ideal microstructure. The reasonable distribution of carbides in the austenite matrix is beneficial to improve the wear resistance of the material. At the same time, it can maintain good strength and toughness and has good comprehensive mechanical properties. It can ensure the hammer works safely under bad working conditions.
Based on the test results, we choose the 1100 ℃ carry out water toughening treatment
Key points of production process control for manganese steel hammer
The hammers of more than 90 kg must be safe and reliable in use and have good wear resistance, so the production process should be strictly controlled.
Smelt
This material is suitable for electric arc furnace and medium frequency induction furnace smelting, chemical composition should be strictly controlled, especially P, s content should not exceed the standard. The scrap should be clean and free of rust. The furnace charge and alloy should be baked above 400 ℃ in the later stage. The cold bending test should be carried out before tapping. The tapping temperature should be strictly controlled at 1 460 ~ 1 500 ℃.
Casting
The casting process is vertical pouring, and the surface of the mold is coated with an alcohol-based quick-drying magnesium oxide coating. In order to refine the grain and improve the surface quality, the pouring temperature should be strictly controlled between 1 430 ℃ and 1 460 ℃.
Heat treatment
Heat treatment is the guarantee to obtain the best performance of the material, and the production should be carried out in strict accordance with the process (see Figure 1).
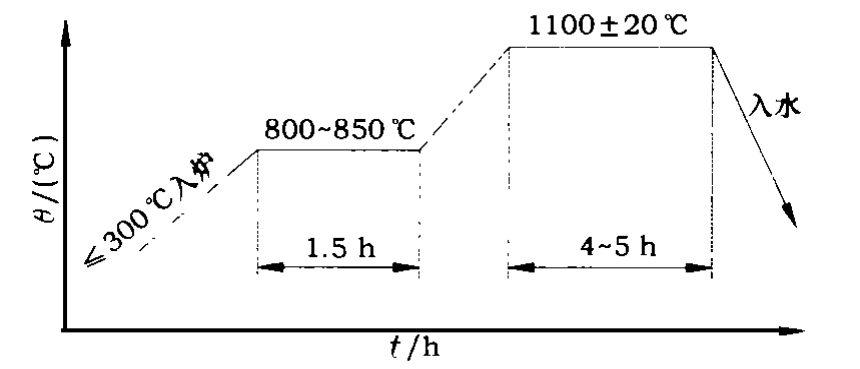
Figure 1. 90kg manganese steel hammer heat treatment
Checking
The manganese steel hammer shall not have any casting defects that affect its performance, such as shrinkage cavity, shrinkage porosity, internal and external cracks, etc. Ultrasonic inspection must be carried out one by one before leaving the factory.
Manganese steel hammer by Qiming Casting®
When it comes to manganese steel hammers, Qiming Casting had manufactured those wear parts for hammer mill, shredder, and cement customers. All Qiming Casting Replacement Parts are backed by ISO9001:2015 quality control system and are shipped only after meeting our rigorous quality standards. We are committed to meeting your replacement parts needs in a professional and efficient manner. Our Customer Support Department is ready to help you with a quote, to check inventory, or simply answer a technical question. Talk to your Qiming Casting professional today about your specific needs!
[wpforms id=”3777″]