Some factors for crusher part useful life
Some customers (the crusher plant users and new traders) often ask us these questions: How long is your products useful life? Which material is the best choice? Are the Mn18 better than Mn13? What is the different between Mn13 and Mn18?
As a casting worker,I want to share my experience about crusher part useful life factors. The crusher part which we discuss just the casting wear parts(manganese casting parts and chrome casting parts, such as jaw plate,cone liner, roll mill liner,etc)
1. Crusher Part Material Choice.
Except for blow bar, most of crusher parts are manufactured by manganese steel (The blow bars material is high manganese). Three trademarks in manganese steel.Mn14,Mn18 and Mn22. When high manganese steel get huge impact or crush stress, its surface will harden very quickly, at the same time, its body still have good toughness.So the surface harden more adequate, the better of wear.High manganese steel has a low hardness(HB170-230),when the uncured wear is extremely limited, the surface is not sufficiently hardened(full hardened surface hardness more then HB550,if not full, it will less than HB350), the wearable can not promise.
So which material is the best choice based on which products you crushed. For manganese casting foundry, the abandoned manganese steel can reach the “Mn” elements content. However, if need 18% content or more, electrolysis manganese is the only choice.
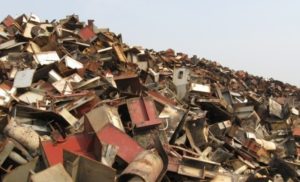
abandoned manganese steel
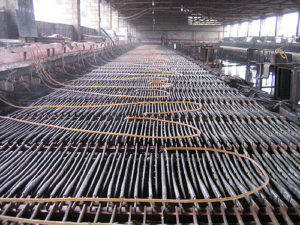
electrolysis manganese
2. Heat Treatment
The most important step in casting, which direct to effect product quality.Before heat treatment, the casting surface must clear;strictly control the time from casting furnace to water pool;decrease the content of carbon on the surface of product;also need care about the water pool temperature(European’s standard,the water pool temperature must lower than 20*c)………
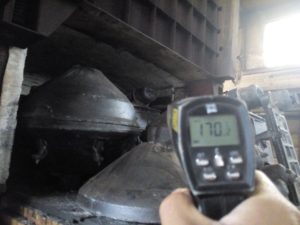
Temperature control when we put the castings into heat treatment furnace.
3. Machining and Printing.
After heat treatment, the castings will be send to machining work shop to machining, so as to correct the casting size and suit for crusher plant. At the last step, printing no only make them beautiful,but also protect them from oxidation.