Our Russia customer wants Qiming Casting to manufacture a set (84 pcs) Mn13Mo1 apron feeder flights to exchange the old flights. Apron feeder flights are also called apron feeder pans, which are the main wear exchange parts in the apron feeder. In simple terms, an apron feeder (also known as a pan feeder) is a mechanical type of feeder used in material handling operations to transfer (feed) material to other equipment or extract material (ore/rock) from storage stockpiles, bins, or hoppers at a controlled rate of speed.
Basic Technical Parameters
- Weight: 535kg
- Material: Mn13Mo1
- Length: 2740mm
- Weight: 456mm
- Height: 288mm
- Thickness: 30mm-55mm
- 8 unmachined assembly holes on both sides
Gating System And Riser Technology
The single piece of apron feeder flights produced this time weighs 535 kg. In order to ensure the smooth and rapid flow of molten steel into the cavity, according to the material and structural characteristics of the casting, the inner runner of the casting uses a flat gate, which is concentrated on one side of the casting It is divided into 4 channels to form an open gating system and then introduced into the casting cavity. And set up an air channel on the opposite side of the runner away from the riser to prevent the casting from being insufficiently poured. According to the actual production situation, the filling of molten steel was observed to be stable, and no casting defects such as insufficient pouring and cold barriers were found.
In order to obtain excellent castings with dense structure and no defects, especially to avoid the defects of the coarse structure under the riser of manganese steel, strengthen the feeding effect of the casting and reduce the difficulty of subsequent processing of the riser, considering the overall structure and local characteristics of the casting, place the riser The time is mainly concentrated on the flat hot section of the parting surface of the casting, using 4 special risers for heating and necking, and the layout of the gating system is shown in the following figure.
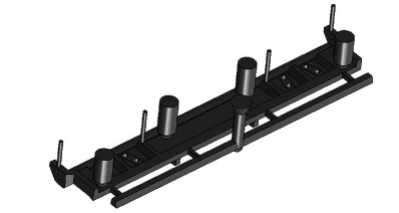
Apron Feeder Flights Gating System
Scale Control
Castings require dimensional tolerances to implement CT8 standards. Combining the characteristics of the casting: the length and size control requirements are strict, no overlength is allowed, and the lower baffle is not processed but must be coordinated with the host, making the size control of the casting more difficult. The selection of scale is particularly important in this type of casting. In combination with the company’s production status and the characteristics of the molding material, different scales are selected for the scale of the casting’s length, width, height, and different parts of the casting. The length of the casting is large, the scale is selected within the range of 2.8% to 3.4%, the width and height scale is selected within the range of 2.2% to 2.6%, and the scale of the casting where the casting hinders shrinkage is selected within the range of 1.8% to 2.2% Within the scope, in addition, according to the actual production situation, it is necessary to set the process correction amount in the casting part according to the structural characteristics of the casting to make up for the problems caused by improper scale control.
Melting and Pouring Process
The steel grade of the casting material is smelted in an electric arc furnace, and an alkaline furnace lining is used. Oxygen blowing at the initial stage for decarburization, and later alloying treatment is carried out to produce molten steel with a satisfactory composition. See Table 1 for the chemical composition of these apron feeder flights. Combining the characteristics of the castings, the castings are planned to be poured with a low-temperature quick-casting scheme.
Table 1: The Chemical Composition of Apron Feeder Flights (%) | |||||||
Material | C | Mn | Si | P | S | Cr | Mo |
Mn13Mo1 | 0.91 | 12.84 | 0.48 | 0.046 | 0.005 | 0.41 | 0.89 |
After the later tapping, it should be left in the ladle for sufficient time, and the molten steel should be poured when the temperature of the molten steel has dropped to a suitable temperature. After pouring, in order to make the molten steel in the riser overheat enough to ensure that the casting has enough molten steel for feeding, thermal insulation covering agent is sprinkled above the molten steel in the riser.
In order to meet the actual production situation, it was decided to adopt a pouring plan of pouring multiple pieces in one furnace. During pouring, the pouring temperature should be controlled between 1 410 ℃ and 1 450 ℃, and the lower pouring temperature should be controlled as far as possible, so as to obtain good quality castings.
Heat Treatment Process and Tooling
In view of the fact that the delivery state of the castings is delivered after heat treatment (water toughening treatment), the heat treatment process control of the castings has an extremely critical effect on the deflection deformation of the castings. When the apron feeder flights are heat-treated, the process adopts the typical water toughening process of manganese steel parts. The heat treatment process is placed on a special water toughening treatment chassis, the key parts of the castings are supported smoothly, and the local gaps on the facade should be plugged with insulation materials to reduce the deformation of the castings as much as possible. as the picture shows.

Apron Feeder Flights Heat Treatment
The Results
Through the analysis of the characteristics and difficulty of the casting technology of apron feeder pans castings, the production adopts technical measures such as pattern plate pattern, insulation riser, resin sand molding, electric arc furnace smelting, and special heat treatment tooling, which solves the problem of flights casting. The technical difficulties in production have successfully produced qualified products that meet the requirements of customers. Through the use of customers, such castings can replace imported castings. The results showed that the production process and process control not only reduced casting defects, increased the qualified rate of finished castings, and improved product quality.