Конструкция футеровок шаровых мельниц из низколегированной стали
Основная функция футеровки шаровой мельницы заключается в защите мельницы и использовании выпуклого пика футеровки для удара шаром для измельчения и раздавливания материала. Поэтому основной вид отказа футеровки - абразивный износ при многократных воздействиях малой энергии. В условиях абразивного износа износостойкость напрямую влияет на срок службы деталей, поэтому исследования износостойкости также являются важной технической проблемой. Этот проект выдвигается для разрушения футеровки в условиях абразивного износа, и его цель состоит в том, чтобы улучшить комплексные характеристики износостойкого материала из низколегированной стали в этих условиях.
Низколегированная сталь Вкладыши для шаровых мельниц Анализ материала
Износостойкие низколегированные стальные материалы обычно содержат легирующие элементы, такие как кремний, марганец, хром, молибден, никель и т. Д. Сильное влияние этих легирующих элементов на матричную структуру и способность материала к упрочнению может проявляться в полной мере, что может сделать материал более износостойким.
Углерод: Углерод является важным элементом, влияющим на прочность, твердость, ударную вязкость, прокаливаемость и износостойкость литой стали. Если содержание углерода слишком велико, твердость высокоуглеродистого мартенсита, образованного после термообработки, будет высокой, но ударная вязкость будет низкой, и во время термической обработки легко образуются трещины; если содержание углерода слишком низкое, закаливаемость и твердость отливки будут плохими, а износостойкость - плохой. Принимая во внимание комбинацию твердости и ударной вязкости, в этом материале были приняты два различных содержания углерода (массовая доля, указанная ниже), которые составили 0.30–0.35% и 0.40–0.45% соответственно. Изучено влияние двух содержаний углерода на микроструктуру и свойства низколегированной стали.
Хром: Хром - один из основных элементов износостойких материалов. Его основная функция - улучшить закаливаемость стали, упрочнить матрицу раствором, улучшить стойкость стали к окислению и повысить ее коррозионную стойкость. Хром и железо образуют сплошной твердый раствор и образуют различные соединения с углеродом. Сложный карбид хрома оказывает значительное влияние на свойства стали, особенно на улучшение износостойкости. Cr и Fe образуют интерметаллическое соединение FeCr. Хром может значительно повысить закаливаемость стали, но он также имеет тенденцию к увеличению отпускной хрупкости стали. Хром улучшает отпускную хрупкость стали и снижает мартенситную точку ms стали. Когда хром добавляется в чистое железо и сталь, прочность и твердость могут быть улучшены при определенном содержании хрома. Учитывая влияние хрома на микроструктуру и свойства стали, содержание хрома составляет 1.0% ~ 1.4%. Влияние хрома на микроструктуру и свойства стали наблюдается экспериментально.
Никель: Никель и углерод не образуют карбидов. Они являются основными легирующими элементами для формирования и стабилизации аустенита. В этом отношении роль уступает только углероду и азоту. Никель и железо существуют в α-фазе и γ-фазе стали в форме взаимной растворимости, что делает их более прочными. За счет уменьшения размера зерна α-фазы улучшаются низкотемпературные свойства, особенно вязкость стали. Никель может улучшить закаливаемость стали за счет снижения критической температуры превращения и скорости диффузии элементов в стали. Некоторые физические свойства стали и сплава могут быть значительно улучшены при высоком содержании никеля. Влияние никеля на ударную вязкость, пластичность и другие технологические свойства стали меньше, чем у других легирующих элементов. Кроме того, поскольку никель является редким элементом и важным стратегическим материалом, содержание никеля установлено на уровне 0.4% с учетом вышеуказанных факторов.
Молибден: Молибден относится к элементу замкнутой области γ-фазы. Молибден существует в фазе твердого раствора и в фазе карбида в стали. В карбидной фазе, когда содержание Мо низкое, он образует композитный цементит с железом и углеродом; при высоком содержании образует свой особый карбид. Влияние молибдена на сталь можно резюмировать как улучшение прокаливаемости, повышение термической прочности, предотвращение отпускной хрупкости, повышение остаточной намагниченности и коэрцитивности, улучшение коррозионной стойкости сплава в некоторых средах и предотвращение тенденции к точечной коррозии. Молибден оказывает упрочняющее действие на феррит и улучшает стабильность карбидов, поэтому он благоприятно влияет на прочность стали. Влияние молибдена на термическое охрупчивание стали довольно сложно. Как отдельный элемент сплава, Мо увеличивает отпускную хрупкость стали, но когда он сосуществует с другими элементами, такими как хром и марганец, молибден снижает или подавляет отпускную хрупкость, вызванную другими элементами. Поскольку различное содержание молибдена может по-разному влиять на свойства стали, мы решили выбрать содержание молибдена в эксперименте как 0.25% - 0.35% и 0.45% - 0.60%.
Марганец: Марганец является хорошим раскислителем и обессеривается. Марганец и железо образуют твердый раствор, улучшающий твердость и прочность феррита и аустенита в стали; в то же время это карбидообразующий элемент, который входит в цементит и замещает некоторые атомы железа. Марганец может очищать перлит и косвенно повышать прочность перлитной стали за счет снижения критической температуры превращения. Марганец также может значительно снизить температуру AR1 и скорость разложения аустенита в стали. Марганец оказывает значительное влияние на повышение прочности низко- и среднеуглеродистых перлитных сталей. Однако как легирующий элемент марганец имеет свои недостатки. Когда содержание Mn выше, размер зерна стали имеет тенденцию к укрупнению и повышается чувствительность к отпускной хрупкости. Белые пятна на стали легко образуются из-за неправильного охлаждения после плавки, литья и ковки. Учитывая влияние марганца на микроструктуру и свойства стали, содержание марганца составляет 1.1% 1.4%.
Кремний: Кремний - один из распространенных элементов стали. Содержание кремния в стали как легирующего элемента должно быть не менее 0.40%. Кремний не образует карбид в стали, но существует в феррите или аустените в виде твердого раствора. Он улучшает прочность твердого раствора в стали, а его скорость деформационного упрочнения холодной деформацией очень высока, уступая только фосфору, но также в определенной степени снижает ударную вязкость и пластичность стали. Если содержание кремния превышает 3%, пластичность, ударная вязкость и пластичность стали значительно снизятся. Кремний может улучшить предел упругости, предел текучести, коэффициент текучести, усталостную прочность и коэффициент усталости стали. Кремний может повысить температуры отжига, нормализации и закалки стали, снизить скорость диффузии углерода в феррите и повысить стабильность стали при отпуске. Учитывая влияние кремния на свойства и микроструктуру стали, диапазон содержания кремния составляет 1.1% 1.4%.
Редкоземельный: Редкоземельные элементы в стали выполняют две основные функции: очистка и легирование. Re может улучшить микроструктуру отливки, уменьшить размер зерна, очистить расплавленную сталь, модифицировать неметаллические включения, улучшить их морфологию и распределение, а также сыграть роль в микролегировании. Повышение ударной вязкости и литейных свойств (стойкость к образованию горячих трещин и текучесть), повышение прочности. Однако из-за неопределенности метода и количества добавления, если содержание редкоземельных элементов слишком велико, это может отрицательно сказаться на свойствах стали. Следовательно, содержание редкоземельных элементов в этом материале определено на уровне 0.04% - 0.06%.
Бор: Выдающаяся функция бора в стали заключается в том, что закаливаемость стали можно повысить за счет небольшого количества бора (0.001%). Когда содержание бора превышает 0.007%, это приведет к горячему охрупчиванию стали. Следовательно, содержание бора в этом материале определено равным 0.003%.
Основные элементы экспериментальных материалов были выбраны в соответствии с приведенным выше анализом. Содержание углерода в образцах №1 и №2 составляет 0.30–0.35%, а содержание молибдена - 0.25–0.35%; содержание углерода в образцах № 3 и № 4 составляет 0.40–0.45%, а содержание молибдена составляет 0.45–0.60%.
Процесс литья гильз для шаровых мельниц из низколегированной стали
В этом эксперименте для плавки используется индукционная печь средней частоты мощностью 50 кВт. Чтобы уменьшить окисление шихты, следует по возможности избегать перемешивания расплавленного металла. На более поздней стадии плавки подающий блок не должен быть слишком большим и должен быть высушен до определенной температуры, чтобы предотвратить разбрызгивание у горловины печи. Последовательность подачи: стальной лом, чугун → никелевый лист, феррохром, ферромолибден → ферросилиций, ферромарганец → редкоземельный ферросилиций и, наконец, добавление алюминия для раскисления.
После сухого перемешивания в течение 2-3 минут формовочный песок смешивали с водой и стеклом в течение 4-6 минут. После изготовления пресс-формы ее затвердевают продувкой углекислым газом (давление выдувания 0.15-0.25 МПа, время выдувания 1-2 мин). Перед заливкой песчаная форма и сплав предварительно нагреваются в печи и остаются сухими. Температура предварительного нагрева составляет около 100 ℃.
Термическая обработка футеровок шаровых мельниц из низколегированной стали
Свойства литых материалов должны подвергаться надлежащей термообработке. В фактических рабочих условиях должна быть получена мартенситная структура с высокой твердостью, высокой прочностью и хорошей ударной вязкостью, и применяется процесс термообработки закалки и отпуска. Переохлажденный аустенит низколегированной износостойкой стали относительно стабилен, а скорость охлаждения масла в низкотемпературной зоне намного меньше, чем у воды, поэтому масло является наиболее подходящей закалочной средой. Отпуск предназначен для уменьшения или устранения остаточного напряжения, вызванного закалкой, улучшения пластичности и ударной вязкости материала, уменьшения его хрупкости и получения соответствующей комбинации пластичности, ударной вязкости и твердости. Поэтому выбираются температуры закалки 850, 880, 910 и 930 ℃ на 1 час. Температура отпуска составляет 200, 230, 260 и 290 ℃, время выдержки - 2 часа.
Испытание рабочих характеристик футеровок шаровых мельниц из низколегированной стали
Твердость образцов измеряли с помощью твердомера по Роквеллу hr-150, а микроструктуру наблюдали с помощью металлографического микроскопа Olympus BH-2.
Табл.1 Твердость образцов в литом состоянии (HRC) | ||||
Образец | Первая точка | Вторая точка | Третья точка | Ср. |
#1 | 31 | 36 | 35 | 34 |
#2 | 31 | 35.5 | 37 | 34.5 |
#3 | 38 | 39 | 40 | 39 |
#4 | 39 | 38.5 | 41 | 39.5 |
Из таблицы 1 видно, что значения твердости образцов №1 и №2 практически одинаковы, но с увеличением содержания углерода твердость образцов №3 и №4 явно возрастает.
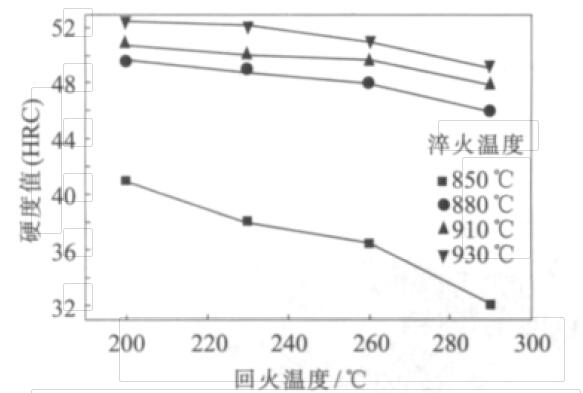
Рис.1 Твердость образца №1 при различной температуре термообработки.
Из рис.1 видно, что на каждой кривой температуры закалки с повышением температуры отпуска значение твердости образца № 1 в основном имеет тенденцию к снижению, но диапазон снижения не очень велик, а тенденция к снижению относительно нежный; на кривой ударной вязкости с повышением температуры закалки значение уменьшается, но с повышением температуры отпуска его значение увеличивается. С повышением температуры отпуска содержание углерода, содержание легирующих элементов, плотность дислокаций и число двойников в мартенситной матрице уменьшаются, поэтому степень упрочнения также уменьшается, поэтому уменьшается твердость. С повышением температуры отпуска происходит перекристаллизация матрицы и точечное огрубление и сфероидизация карбида. Поскольку сфероидизация карбидов уменьшает расстояние скольжения дислокаций и делает расстояние скольжения короче, дислокация не может их разрезать, поэтому ударная вязкость имеет тенденцию к увеличению.
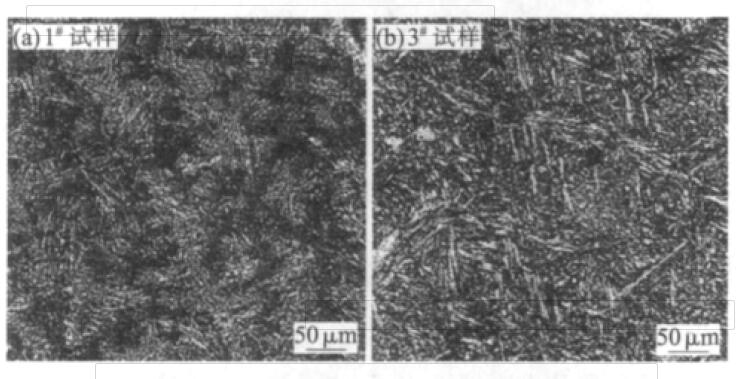
Рис.2 Микроструктура литых образцов №№ 1 и 3
Из рис.2 видно, что микроструктура образцов №1 и №3 представляет собой перлитный。
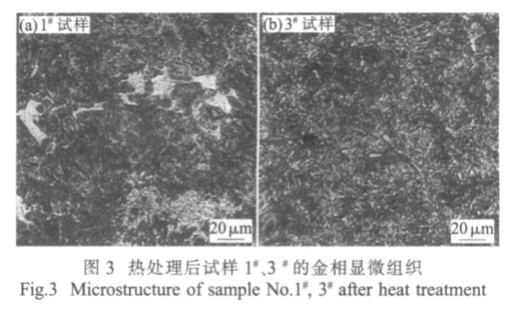
Рис.3 Микроструктура образцов №№ 1 и 3 после термообработки.
На рис. 3 показана металлографическая структура образца после закалки при 910 ℃ и отпуска при 230 ℃. Видно, что микроструктура и матрица двух типов образцов представляют собой реечный мартенсит. Микроструктура образца однородна, размер зерна мелкий.
Таб.2 Результаты эксперимента по ношению после термообработки | |||||
Образец | Сначала худеем, вес / г | Похудеть ж / г | Средн. Похудеть ж / г | Твердость (HRC) | Износостойкость |
#1 | 0.04013 | 0.03705 | 0.03859 | 50 | 25.91345 |
#2 | 0.03874 | 0.03615 | 0.03744 | 51.3 | 26.7094 |
#3 | 0.03091 | 0.03461 | 0.03276 | 53.6 | 30.52503 |
#4 | 0.03288 | 0.0245 | 0.02869 | 55.5 | 34.85535 |
Из таблицы 2 видно, что с увеличением твердости износостойкость образцов №1 - №4 в свою очередь возрастает. Таким образом, можно сделать вывод, что потери материалов при износе напрямую связаны с их твердостью. Чем выше твердость, тем меньше потеря веса, тем выше износостойкость материалов. Кроме того, диспергированные карбиды в матрице также способствуют износостойкости материалов, но этот эффект меньше, чем эффект твердости из-за небольшого количества выделившихся карбидов.
Итоги
- Гильзы шаровых мельниц из низколегированной стали, исследованные в этой статье, обладают высокой закаливаемой способностью и стабильностью при отпуске.
- После закалки при 850-930 ℃ и отпуска при 200-290 ℃ получается тонко отпущенный реечный мартенсит, который придает стали высокую прочность, высокую вязкость и высокую износостойкость.
- Чем выше твердость, чем меньше потеря веса, тем лучше износостойкость.
Об авторе:
Производитель футеровок для мельниц в Китае, Qiming Machinery является лидером в разработке, производстве и поставке футеровок для мельниц для переработки полезных ископаемых и разработки карьеров. Он предлагает клиентам комплексные решения для износостойких футеровок для мельниц, которые повышают производительность, доступность оборудования и снижают затраты на техническое обслуживание. Футеровки мельниц также проходят испытания на устойчивость к уровню кислотности различных элементов, которые могут присутствовать в процессе измельчения. Более длительный срок службы вашего станка означает меньшие расходы и большую прибыль или доход для вашей компании.