Сравнение поведения коррозионной ударной абразии между низкоуглеродистой легированной сталью и сталью с высоким содержанием марганца
Условия работы футеровки мельницы мокрого помола на металлургических рудниках тяжелые, и она не только подвергается коррозии со стороны пульпы с высоким рН, но и изнашивается рудой и мелющими шарами. Кроме того, руда и мелющие шары, падающие на определенную высоту, также оказывают определенное воздействие на футеровочную плиту. В настоящее время основным материалом мельничных футеровок, используемым в Китае, по-прежнему является ZGMn13, но в этих условиях эксплуатации из-за недостаточного упрочнения и плохой коррозионной стойкости высокомарганцовистой стали срок службы футеровки очень короткий, обычно 4-6 месяцев. . Хотя такие материалы, как модифицированная сталь с высоким содержанием марганца и сталь со средним содержанием углерода, были разработаны в стране и за рубежом в последние годы, эффект все еще неудовлетворителен. С другой стороны, исследования механизма коррозии и изнашивания в ударных условиях проводятся редко, что имеет положительное значение для разработки качественных футеровочных материалов. Ударная коррозия и износостойкость недавно разработанной низкоуглеродистой высоколегированной стали (например, Труба ASTM A335 P91) материал футеровки был испытан в смоделированных рабочих условиях и сравнен с текущим основным материалом из высокомарганцовистой стали для футеровки. Ударно-коррозионный механизм изнашивания стали и его изменение во времени.
Сравнение химического состава и механических свойств двух материалов
Материалы | Химический состав% | Механические свойства | |||||||||
C | Mn | Кр` | Ni | Mo | Si | S | P | HRC | Ак/Дж*см² | ||
Низкоуглеродистая легированная сталь | 0.15-0.3 | – | 7.0-10.0 | 1.5-2.0 | 0.7-1.0 | 0.3-0.6 | ≤0.035 | ≤0.035 | 48-51 | > 50 | |
ЗГМн13 | 1.1-1.3 | 12.0-14.0 | – | – | – | 0.3-0.8 | ≤0.03 | ≤0.07 | <21 | > 147 |
Испытание на износ
Испытание на ударную коррозию и износ проводили на модифицированной машине для испытаний на ударную коррозию и износ МДЛ-10, частота ударов которой составляла 200 раз/мин. Исследуемый образец перерабатывается в блок размером 10 мм * 10 мм * 30 мм методом резки проволоки; он установлен на ползун и совершает возвратно-поступательные движения вместе с ползунком во время испытания. Шлам непрерывно поступает на ударную поверхность через перемешивающее устройство. Из текущих исследований абразивов испытания с рудами с определенным диапазоном абразивных свойств могут эффективно оценивать износостойкость материалов, а абразивы в промышленных системах в основном представляют собой руды. Наоборот, использование абразивов со слишком жесткими характеристиками может вызвать ложное впечатление. Поэтому в этом эксперименте в качестве суспензии была выбрана кислотная суспензия железной руды, аналогичная фактическим рабочим условиям, которая была приготовлена из водного раствора серной кислоты с рН=3 и железной руды 6-10 меш. Учитывая дробление и изменение размера частиц руды и ослабление кислотности в тесте, поведение материала при износе может сильно измениться, поэтому руда обновляется каждые 0.5 часа, и одновременно корректируется значение pH. По характеристикам малоэнергетического удара в шаровой мельнице мы выбрали энергию удара равной 2.7 Дж и скорректировали энергию удара по времени в зависимости от укорочения образца в процессе испытания.
Перед каждым испытанием образцы очищали ацетоном в ультразвуковой мойке, затем сразу высушивали, после чего взвешивали на аналитических весах с точностью 0.00001 для получения исходной массы W0, после чего образцы устанавливали в машину для ударной коррозии. и испытания на износ. Образец носили в общей сложности 16 часов, в течение которых образец очищали и взвешивали каждые 2 часа, записывая как Wi (i=2, 4, 6…16), и рассчитывали кумулятивную потерю веса в каждый момент времени △ Wi=W0 -Wi, среднее значение △Wi трех образцов брали для измерения стойкости материала к ударной коррозионной износостойкости. Наконец, Hitachi-X-650 использовали для наблюдения за морфологией поверхности в результате ударного коррозионного износа, а оптический микроскоп Olympus PME использовали для наблюдения за поверхностью, перпендикулярной износостойкости. Проанализированы изменения состояния поверхностного слоя и подповерхностного слоя поверхности, проанализирован механизм ударно-коррозионного изнашивания.
Результаты испытаний и анализ
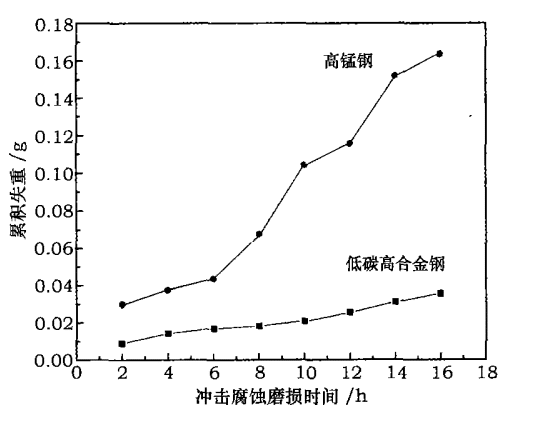
Коррозионно-ударный износ двух сталей в зависимости от времени
Сравнивая кривые кумулятивной потери веса двух сталей при ударном коррозионном износе, можно увидеть, что с увеличением времени ударного коррозионного износа потеря веса двух сталей постоянно увеличивается.
В то же время потеря веса низкоуглеродистой и высоколегированной стали всегда ниже, чем у стали с высоким содержанием марганца, и это преимущество становится все более и более очевидным с течением времени, указывая на то, что стойкость к ударной коррозии низкоуглеродистой стали высока. легированная сталь значительно лучше, чем у высокомарганцовистой стали. Высокомарганцевая сталь. Этот результат показывает, что характеристики износа при ударной коррозии представляют собой всеобъемлющий показатель ударной, коррозионной и износостойкой стойкости материалов, и можно определить взаимодействие трех, а не одного показателя. Соответствующие исследования показали, что взаимодействие между коррозией и износом намного выше, чем сумма их индивидуальных эффектов, а давление вспашки и трещины, вызванные ударом, в значительной степени способствуют коррозии и износу. Реечная мартенситная структура низкоуглеродистой и высоколегированной стали обеспечивает хорошее сочетание твердости и ударной вязкости, а однофазная матрица и высокое содержание хрома обеспечивают ее коррозионную стойкость. Хотя сталь с высоким содержанием марганца обладает высокой ударной вязкостью, она имеет плохую коррозионную стойкость и низкую начальную твердость и не способствует ударному износу после сильной деформации и закалки, что приводит к снижению ее общих характеристик ударной коррозии.