Наш заказчик из России хочет, чтобы компания Qiming Casting изготовила набор (84 шт.) Перронных фидеров Mn13Mo1 для замены старых. Перронные фидерные рейсы также называют фартуковые фартуки, которые являются основными изнашиваемыми деталями в фартук кормушки. Проще говоря, пластинчатый питатель (также известный как лотковый питатель) - это механический питатель, используемый в операциях по перемещению материалов для передачи (подачи) материала на другое оборудование или извлечения материала (руды / породы) из складских складов, бункеров или бункеры с контролируемой скоростью.
Основные технические параметры
- Вес: 535kg
- Материал: Mn13Mo1
- Длина: 2740mm
- Вес: 456mm
- Высота: 288mm
- Толщина: 30 мм-55 мм
- 8 необработанных монтажных отверстий с обеих сторон
Система вентиляции и технология подъема
Изготовленная на этот раз цельная часть фартуков-фидеров весит 535 кг. Чтобы обеспечить плавный и быстрый поток расплавленной стали в полость, в зависимости от материала и конструктивных характеристик отливки, внутренний желоб отливки использует плоский затвор, который сосредоточен на одной стороне отливки. в 4 канала для образования открытой литниковой системы, а затем вводится в литейную полость. И создайте воздушный канал на противоположной стороне желоба от стояка, чтобы предотвратить недостаточную заливку отливки. В соответствии с реальной производственной ситуацией, заполнение жидкой сталью было стабильным, и не было обнаружено никаких дефектов литья, таких как недостаточная разливка и холодные барьеры.
Чтобы получить отличные отливки с плотной структурой и без дефектов, особенно во избежание дефектов грубой структуры под стояком из марганцевой стали, усилить подающий эффект отливки и уменьшить сложность последующей обработки стояка с учетом общего структура и местные характеристики отливки, размещение стояка Время в основном сосредоточено на плоском горячем участке разделяющей поверхности отливки с использованием 4 специальных стояков для нагрева и образования шейки, а схема литниковой системы показана ниже фигура.
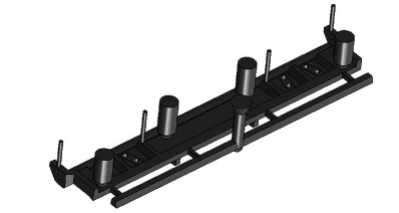
Система стробирования полетов на перроне
Управление масштабом
Отливки требуют допусков на размеры для соответствия стандартам CT8. Сочетание характеристик отливки: требования к контролю длины и размера строгие, превышение длины не допускается, а нижняя перегородка не обрабатывается, но должна согласовываться с хостом, что затрудняет контроль размера отливки. Выбор масштаба особенно важен при этом виде литья. В сочетании с производственным статусом компании и характеристиками формовочного материала выбираются различные шкалы для масштаба длины, ширины, высоты отливки и различных частей отливки. Длина отливки большая, масштаб выбран в диапазоне от 2.8% до 3.4%, масштаб ширины и высоты выбран в диапазоне от 2.2% до 2.6%, а масштаб отливки, в котором отливка препятствует усадке выбирается в диапазоне от 1.8% до 2.2% В рамках объема, кроме того, в соответствии с реальной производственной ситуацией, необходимо установить величину корректировки процесса в литой детали в соответствии с конструктивными характеристиками отливки, чтобы компенсировать проблемы, вызванные неправильным контролем масштаба.
Процесс плавления и разливки
Марка стали литейного материала выплавляется в дуговой электропечи, применяется щелочная футеровка печи. На начальном этапе для обезуглероживания и последующей обработки легированием проводится продувка кислородом для получения жидкой стали удовлетворительного состава. См. Таблицу 1 с химическим составом этих перронных фидерных маршей. Сочетая характеристики отливок, отливки планируется разливать по низкотемпературной схеме быстрой заливки.
Таблица 1: Химический состав перронных фидеров (%) | |||||||
Материалы | C | Mn | Si | P | S | Cr | Mo |
Mn13Mo1 | 0.91 | 12.84 | 0.48 | 0.046 | 0.005 | 0.41 | 0.89 |
После последующего выпуска ее следует оставить в ковше на достаточное время, а жидкую сталь следует вылить, когда температура жидкой стали упадет до подходящей температуры. После заливки, чтобы расплавленная сталь в стояке перегрелась, чтобы обеспечить достаточное количество расплавленной стали для подачи, поверх расплавленной стали в стояке разбрызгивается теплоизоляционный покрывающий агент.
Чтобы соответствовать реальной производственной ситуации, было решено принять план разливки нескольких изделий в одной печи. Во время разливки температура разливки должна находиться в пределах от 1 410 ℃ до 1 450 ℃, а более низкая температура разливки должна контролироваться, насколько это возможно, для получения отливок хорошего качества.
Процесс термической обработки и оснастка
Ввиду того факта, что состояние поставки отливок достигается после термообработки (закалка в воде), контроль процесса термообработки отливок имеет чрезвычайно важное влияние на деформацию прогиба отливок. Когда лопасти питателя фартука подвергаются термообработке, используется типичный процесс водной закалки деталей из марганцовистой стали. Процесс термообработки проводится на специальном шасси для водоупрочненной обработки, ключевые части отливок имеют плавную опору, а местные зазоры на фасаде должны быть закрыты изоляционными материалами, чтобы максимально снизить деформацию отливок. как показано на картинке.

Термическая обработка полетов фартука питателя
Результаты
Благодаря анализу характеристик и сложности технологии литья отливок фартуков питателя, производство принимает такие технические меры, как узорная пластина, изоляционный стояк, формование смоляного песка, плавка в электродуговой печи и специальные инструменты для термообработки, которые решают проблема литья полетов. Технические трудности в производстве позволили успешно производить качественную продукцию, отвечающую требованиям заказчиков. Такие отливки по желанию клиентов могут заменить импортные. Результаты показали, что производственный процесс и контроль процесса не только уменьшили дефекты отливок, повысили качество готовых отливок и улучшили качество продукции.