Порівняння поведінки стирання під впливом корозії між низьковуглецевою легованою сталлю та сталлю з високим вмістом марганцю
Умови роботи футеровок мокрого млина в металургійних шахтах суворі, і вона не тільки піддається корозії целюлозою з сильним рН, але й зношується рудою та мальними кульками. Крім того, певний вплив на підкладкову плиту надають також руда та млільні кульки, які падають на певну висоту. В даний час основним матеріалом вкладишів млинів, який використовується в Китаї, є ZGMn13, але в таких робочих умовах, через недостатнє зміцнення та погану корозійну стійкість високомарганцевої сталі, термін служби футеровки дуже короткий, зазвичай 4-6 місяців. . Хоча такі матеріали, як модифікована сталь з високим вмістом марганцю та середньовуглецеві леговані сталі, були розроблені в країні та за кордоном останніми роками, ефект все ще є незадовільним. З іншого боку, дослідження механізму корозії та зношування в умовах удару є рідкістю, що має позитивне значення для розробки високоякісних футеровочних матеріалів. Ударні корозійні та зношувальні властивості нещодавно розробленої низьковуглецевої високолегованої сталі (наприклад, Труба ASTM A335 P91) матеріал футеровки були випробувані в змодельованих робочих умовах і порівняні з поточним основним матеріалом з високомарганцевої сталі для футеровок. Ударний механізм корозійного зношування сталі та його зміна в часі.
Порівняння хімічного складу та механічних властивостей двох матеріалів
Матеріал | Хімічний склад,% | Механічні властивості | |||||||||
C | Mn | Cr` | Ni | Mo | Si | S | P | HRC | Ak/J*см² | ||
Низьковуглецева легована сталь | 0.15-0.3 | - | 7.0-10.0 | 1.5-2.0 | 0.7-1.0 | 0.3-0.6 | ≤ 0.035 | ≤ 0.035 | 48-51 | > 50 | |
ЗГМн13 | 1.1-1.3 | 12.0-14.0 | - | - | - | 0.3-0.8 | ≤ 0.03 | ≤ 0.07 | <21 | > 147 |
Тест на знос
Випробування на ударну корозію та знос проводили на модифікованій машині для випробування корозії та зносу MDL-10, а частота ударів випробувальної машини становила 200 разів/хв. Зразок, що підлягає випробуванню, обробляється в блок 10 мм * 10 мм * 30 мм методом різання дроту; він встановлений на циліндрі, і під час випробування він обертається вгору і вниз разом з бараном. Суспензія безперервно надходить на поверхню удару через пристрій для перемішування. Згідно з поточними дослідженнями абразивів, випробування рудами з певним діапазоном абразивних властивостей дозволяють ефективно оцінити зносостійкість матеріалів, а абразивами в промислових системах є переважно руди. Навпаки, використання абразивів із занадто жорсткими характеристиками може викликати помилкові враження. Тому в цьому експерименті в якості суспензії було обрано залізорудну кислотну суспензію, подібну до реальних робочих умов, яку готували з водним розчином сірчаної кислоти PH=3 і залізної руди 6-10 меш. Враховуючи подрібнення та зміни розміру руди, а також ослаблення кислотності під час випробування, поведінка матеріалу може сильно змінитися, тому руда оновлюється кожні 0.5 години, а значення pH коригується одночасно. Відповідно до характеристик удару малої енергії в кульовому млині ми обрали енергію удару 2.7 Дж і вчасно відкоригували енергію удару залежно від укорочення зразка під час випробування.
Перед кожним випробуванням зразки очищали ацетоном в ультразвуковому очищувачі, потім відразу сушили, а потім зважували на аналітичних вагах з точністю 0.00001 для отримання вихідної маси W0, а потім зразки встановлювали в машину для ударної корозії. і випробування на знос. Зразок носили загалом 16 годин, протягом яких зразок очищали та зважували кожні 2 години, записували як Wi (i=2, 4, 6…16), і розраховували кумулятивну втрату ваги в кожен момент часу △ Wi=W0 -Wi, середнє значення △Wi трьох зразків було взято для вимірювання ударної корозійної зносостійкості матеріалу. Нарешті, Hitachi-X-650 використовувався для спостереження за морфологією поверхні корозійного зношування, а оптичний мікроскоп Olympus PME використовувався для спостереження за поверхнею, перпендикулярною до зносостійкості. Проаналізовано зміни стану поверхневого шару та підповерхневого шару поверхні та проаналізовано механізм ударно-корозійного зношування.
Результати та аналіз
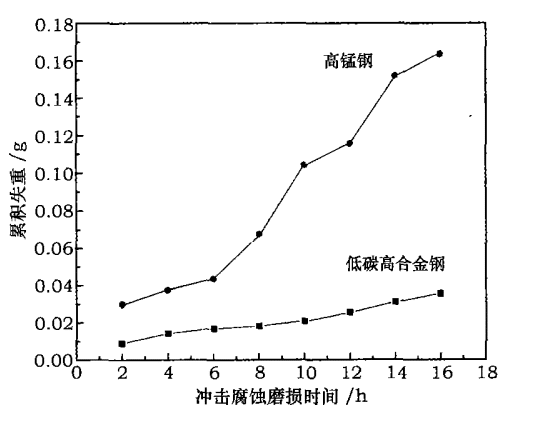
Корозійний удар втрата зносу двох сталей VS час
Порівнюючи кумулятивні криві втрати ваги двох сталей із корозійним зносом від удару, можна побачити, що із подовженням часу ударного корозійного зносу втрата ваги двох сталей постійно зростає.
У той же час втрата ваги низьковуглецевої та високолегованої сталі завжди нижча, ніж у високомарганцевої сталі, і ця перевага стає все більш очевидною з продовженням часу, що вказує на те, що зносостійкість низьковуглецевої сталі з високим рівнем корозії легована сталь значно краща, ніж сталь з високим вмістом марганцю. Сталь з високим вмістом марганцю. Цей результат показує, що ефективність корозійного зносу є комплексним індексом ударної, корозійної та зносостійкості матеріалів, і можна визначити взаємодію трьох, а не одного індексу. Відповідні дослідження показали, що взаємодія між корозією та зносом набагато вище, ніж сума їхніх окремих ефектів, а тиск оранки та тріщини, викликані ударом, значно сприятимуть корозії та зносу. Структура рейкового мартенситу з низьковуглецевої та високолегованої сталі забезпечує гарне поєднання твердості та міцності, а однофазна матриця та високий вміст хрому забезпечують її корозійну стійкість. Незважаючи на те, що сталь з високим вмістом марганцю має високу в’язкість, вона має низьку корозійну стійкість і низьку початкову твердість і не сприяє зносу при ударі після сильної деформації та зміцнення, що призводить до зниження її загальної ефективності корозійного зносу.