Diseño de revestimientos de molino de bolas de acero de baja aleación
La función principal del revestimiento del molino de bolas es proteger el molino y usar el pico convexo del revestimiento para jugar la bola para moler y triturar el material. Por lo tanto, el principal modo de falla del revestimiento es el desgaste abrasivo bajo el impacto repetido de poca energía. Bajo la condición de desgaste abrasivo, la resistencia al desgaste afecta directamente la vida útil de las piezas, por lo que la investigación sobre la resistencia al desgaste también es un problema técnico importante. Este proyecto se presenta por la falla del revestimiento en condiciones de desgaste abrasivo, y el propósito es mejorar el desempeño integral del material resistente al desgaste de acero de baja aleación en esta condición.
Acero de baja aleación Revestimientos de molino de bolas Análisis de Material
Los materiales de acero de baja aleación resistentes al desgaste generalmente contienen elementos de aleación como silicio, manganeso, cromo, molibdeno, níquel, etc. La fuerte influencia de estos elementos de aleación en la estructura de la matriz y la templabilidad del material se puede poner en juego por completo, lo que puede hacer que el material tenga una mejor resistencia al desgaste.
Carbón: El carbono es un elemento importante que afecta la resistencia, dureza, tenacidad, templabilidad y resistencia al desgaste del acero fundido. Si el contenido de carbono es demasiado alto, la dureza de la martensita con alto contenido de carbono formada después del tratamiento térmico es alta, pero la tenacidad es baja y las grietas son fáciles de formar durante el tratamiento térmico; si el contenido de carbono es demasiado bajo, la templabilidad y dureza de la pieza fundida son malas y la resistencia al desgaste es mala. Considerando la combinación de dureza y tenacidad, se adoptaron dos contenidos de carbono diferentes (fracción de masa, la misma a continuación) en este material, que fue 0.30% - 0.35% y 0.40% - 0.45%, respectivamente. Se estudiaron los efectos de dos contenidos de carbono sobre la microestructura y las propiedades del acero de baja aleación.
Cromo: El cromo es uno de los elementos básicos de los materiales resistentes al desgaste. Su función principal es mejorar la templabilidad del acero, fortalecer la matriz por solución, mejorar la resistencia a la oxidación del acero y aumentar su resistencia a la corrosión. El cromo y el hierro forman una solución sólida continua y forman una variedad de compuestos con el carbono. El complejo de carburo de cromo tiene un efecto significativo sobre las propiedades del acero, especialmente la mejora de la resistencia al desgaste. El Cr y el Fe forman el compuesto intermetálico FeCr. El cromo puede aumentar significativamente la templabilidad del acero, pero también tiende a aumentar la fragilidad del acero. El cromo mejora la fragilidad del acero y reduce el punto de martensita del acero. Cuando se agrega cromo en hierro y acero puros, la resistencia y la dureza se pueden mejorar con un cierto contenido de cromo. Teniendo en cuenta el efecto del cromo sobre la microestructura y las propiedades del acero, el contenido de cromo es de 1.0% ~ 1.4%. El efecto del cromo sobre la microestructura y las propiedades del acero se observa mediante experimentos.
níquel: El níquel y el carbono no forman carburos. Son los principales elementos de aleación para formar y estabilizar la austenita. En este sentido, el papel es superado solo por el carbono y el nitrógeno. El níquel y el hierro existen en la fase α y la fase γ del acero en forma de solubilidad mutua, lo que los fortalece. Al refinar el tamaño de grano de la fase α, se mejoran las propiedades a baja temperatura, especialmente la tenacidad del acero. El níquel puede mejorar la templabilidad del acero al reducir la temperatura crítica de transformación y la tasa de difusión de los elementos en el acero. Algunas propiedades físicas del acero y la aleación pueden mejorarse significativamente cuando el contenido de níquel es alto. El efecto del níquel sobre la dureza, la plasticidad y otras propiedades del proceso del acero es menor que el de otros elementos de aleación. Además, como el níquel es un elemento escaso y un material estratégico importante, el contenido de níquel se establece en 0.4% en función de los factores anteriores.
Molibdeno: El molibdeno pertenece al elemento de la región cerrada de la fase γ. El molibdeno existe en la fase de solución sólida y en la fase de carburo en el acero. En la fase de carburo, cuando el contenido de Mo es bajo, forma cementita compuesta con hierro y carbono; cuando el contenido es alto, forma su propio carburo especial. El efecto del molibdeno en el acero se puede resumir en mejorar la templabilidad, mejorar la resistencia térmica, prevenir la fragilidad por temple, aumentar la remanencia y la coercitividad, mejorar la resistencia a la corrosión de la aleación en algunos medios y prevenir la tendencia a la corrosión por picaduras. El molibdeno tiene un efecto de fortalecimiento de la solución sólida sobre la ferrita y mejora la estabilidad de los carburos, por lo que tiene un efecto favorable sobre la resistencia del acero. El efecto del molibdeno sobre la fragilización del acero por temple es bastante complicado. Como un solo elemento de aleación, el Mo aumenta la fragilidad del acero, pero cuando coexiste con otros elementos, como el cromo y el manganeso, el molibdeno reduce o suprime la fragilidad causada por otros elementos. Debido a que el diferente contenido de molibdeno puede tener diferentes efectos sobre las propiedades del acero, decidimos seleccionar el contenido de molibdeno en el experimento como 0.25% - 0.35% y 0.45% - 0.60%.
manganeso: El manganeso es un buen desoxidante y desulfurado. El manganeso y el hierro forman una solución sólida, que mejora la dureza y resistencia de la ferrita y la austenita en el acero; al mismo tiempo, es un elemento formador de carburo, que ingresa a la cementita para reemplazar algunos átomos de hierro. El manganeso puede refinar la perlita y mejorar la resistencia del acero perlítico indirectamente al reducir la temperatura crítica de transformación. El manganeso también puede reducir significativamente la temperatura AR1 y la tasa de descomposición de austenita del acero. El manganeso tiene un efecto significativo en la mejora de la resistencia de los aceros perlíticos de bajo y medio carbono. Sin embargo, como elemento de aleación, el manganeso tiene sus desventajas. Cuando el contenido de Mn es más alto, el tamaño de grano del acero tiende a endurecerse y aumenta la sensibilidad a la fragilidad por temple. Es fácil producir manchas blancas en el acero debido a un enfriamiento inadecuado después de la fundición, fundición y forja. Teniendo en cuenta los efectos del manganeso sobre la microestructura y las propiedades del acero, el contenido de manganeso es del 1.1% ± 1.4%.
Silicio: El silicio es uno de los elementos comunes del acero. Como elemento de aleación, el contenido de silicio en el acero no debe ser inferior al 0.40%. El silicio no forma carburo en el acero, pero existe en la ferrita o austenita en forma de solución sólida. Mejora la resistencia de la solución sólida en el acero, y su velocidad de endurecimiento por deformación por trabajo en frío es muy fuerte, superada solo por el fósforo, pero también reduce la tenacidad y plasticidad del acero hasta cierto punto. Si el contenido de silicio es superior al 3%, la plasticidad, tenacidad y ductilidad del acero se reducirán significativamente. El silicio puede mejorar el límite elástico, el límite de fluencia, el índice de fluencia, la resistencia a la fatiga y el índice de fatiga del acero. El silicio puede aumentar las temperaturas de templado, normalización y templado del acero, reducir la tasa de difusión del carbono en la ferrita y aumentar la estabilidad del templado del acero. Teniendo en cuenta los efectos del silicio sobre las propiedades y la microestructura del acero, el rango de contenido de silicio es del 1.1% ± 1.4%.
Tierra extraña: Hay dos funciones principales de las tierras raras en el acero, una es la purificación y la otra es la aleación. Re puede mejorar la microestructura recién fundida, refinar el tamaño de grano, purificar el acero fundido, modificar las inclusiones no metálicas, mejorar su morfología y distribución y desempeñar un papel en la microaleación. Mejore la tenacidad y las propiedades de fundición (resistencia al agrietamiento en caliente y fluidez), mejore la resistencia. Sin embargo, debido a la incertidumbre de agregar el método y la cantidad, si el contenido de tierras raras es demasiado, puede tener un efecto adverso en las propiedades del acero. Por lo tanto, se determina que el contenido de tierras raras en este material es del 0.04% al 0.06%.
Boro La función sobresaliente del boro en el acero es que la templabilidad del acero se puede aumentar con una pequeña cantidad de boro (0.001%). Cuando el contenido de boro es superior al 0.007%, provocará la fragilización en caliente del acero. Por lo tanto, se determina que el contenido de boro en este material es del 0.003%.
Los principales elementos de los materiales experimentales se seleccionaron de acuerdo con el análisis anterior. El contenido de carbono de las muestras n. ° 1 y n. ° 2 es 0.30% - 0.35%, y el contenido de molibdeno es 0.25% - 0.35%; el contenido de carbono de las muestras # 3 y # 4 es 0.40% - 0.45%, y el contenido de molibdeno es 0.45% - 0.60%.
Proceso de fundición de revestimientos de molino de bolas de acero de baja aleación
En este experimento, se utiliza un horno de inducción de frecuencia media de 50 kW para la fundición. Para reducir la oxidación de la carga del horno, debe evitarse en la medida de lo posible la agitación del metal fundido. En la etapa posterior de la fundición, el bloque de alimentación no debe ser demasiado grande y debe secarse a una cierta temperatura para evitar salpicaduras en la boca del horno. La secuencia de alimentación es chatarra de acero, arrabio → placa de níquel, ferrocromo, ferromolibdeno → ferrosilicio, ferromanganeso → ferrosilicio de tierras raras y, finalmente, adición de aluminio para la desoxidación.
Después de mezclar en seco durante 2-3 min, la arena de moldeo se mezcló con agua y vidrio durante 4-6 min. Una vez hecho el molde, el molde se endurece soplando dióxido de carbono (la presión de soplado es de 0.15 a 0.25 MPa, el tiempo de soplado es de 1-2 min). Antes de verter, el molde de arena y la aleación se precalientan en el horno y se mantienen secos. La temperatura de precalentamiento es de aproximadamente 100 ℃.
Tratamiento térmico de revestimientos de molino de bolas de acero de baja aleación
Las propiedades de los materiales recién fundidos deben tratarse térmicamente adecuadamente. En las condiciones de trabajo reales, se debe obtener la estructura de martensita con alta dureza, alta resistencia y buena tenacidad, y se debe adoptar el proceso de tratamiento térmico de temple y revenido. La austenita subenfriada del acero de baja aleación resistente al desgaste es relativamente estable y la velocidad de enfriamiento del aceite en la zona de baja temperatura es mucho menor que la del agua, por lo que el aceite es el medio de enfriamiento más adecuado. El revenido consiste en reducir o eliminar la tensión residual provocada por el temple, mejorar la plasticidad y tenacidad del material, reducir su fragilidad y obtener la combinación adecuada de plasticidad, tenacidad y dureza. Por lo tanto, se seleccionan las temperaturas de enfriamiento de 850, 880, 910 y 930 ° C durante 1 h. La temperatura de revenido es 200, 230, 260 y 290 ℃, y el tiempo de mantenimiento es de 2 h.
Pruebas de rendimiento de revestimientos de molinos de bolas de acero de baja aleación
La dureza de las muestras se midió con el probador de dureza Rockwell hr-150, y la microestructura se observó con un microscopio metalográfico Olympus BH-2.
Tab.1 Dureza de las muestras recién fundidas (HRC) | ||||
Muestra | Primer punto | Segundo punto | Tercer punto | AVG. |
#1 | 31 | 36 | 35 | 34 |
#2 | 31 | 35.5 | 37 | 34.5 |
#3 | 38 | 39 | 40 | 39 |
#4 | 39 | 38.5 | 41 | 39.5 |
Puede verse en la Tabla 1 que los valores de dureza de las muestras n. ° 1 y n. ° 2 son casi los mismos, pero con el aumento del contenido de carbono, la dureza de las muestras n. ° 3 y n. ° 4 aumenta obviamente.
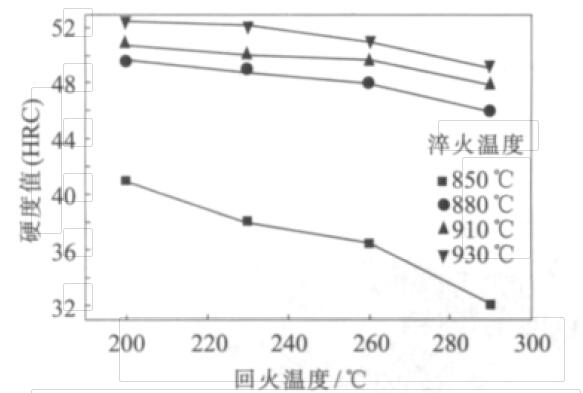
Fig.1 Dureza de la muestra n. ° 1 a diferentes temperaturas de tratamiento térmico
Puede verse en la Fig.1 que, en cada curva de temperatura de temple, con el aumento de la temperatura de revenido, el valor de dureza de la muestra n. ° 1 muestra básicamente una tendencia a la baja, pero el rango de disminución no es muy grande, y la tendencia a la baja es relativamente suave en la curva de tenacidad al impacto, con el aumento de la temperatura de temple, el valor disminuye, pero con el aumento de la temperatura de revenido, su valor aumenta. Con el aumento de la temperatura de revenido, el contenido de carbono, el contenido del elemento de aleación, la densidad de dislocación y el número de macla en la matriz de martensita disminuyen, por lo que la cantidad de refuerzo también disminuye, por lo que la dureza disminuye. Con el aumento de la temperatura de revenido, la recristalización de la matriz y el punto de carburo se engrosan y se esferoidizan. Debido a que la esferoidización de carburo reduce la distancia de deslizamiento de la dislocación y hace que la distancia de deslizamiento sea más corta, la dislocación no puede cortarlos, por lo que la tenacidad muestra una tendencia ascendente.
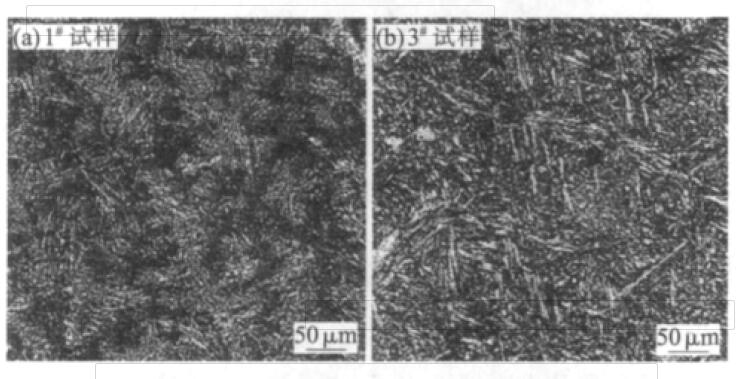
Fig.2 Microestructura de la muestra recién moldeada No. 1 y No. 3
Se puede ver en la Fig.2 que la microestructura de las muestras # 1 y # 3 es perlita。
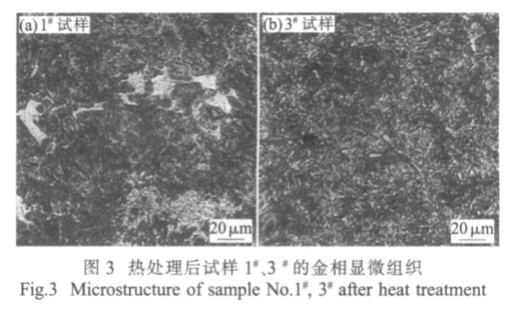
Fig.3 Microestructura de la muestra n. ° 1 y n. ° 3 después del tratamiento térmico
La Figura 3 muestra la estructura metalográfica de la muestra después de templar a 910 ℃ y templar a 230 ℃. Se puede ver que la microestructura y la matriz de los dos tipos de muestras son martensita de listones. La microestructura de la muestra es uniforme y el tamaño de grano fino.
Tab.2 Resultados del experimento de uso después del tratamiento térmico | |||||
Muestra | Primero pierda peso w / g | Bajar de peso w / g | Promedio Bajar de peso w / g | Dureza (HRC) | resistencia al desgaste |
#1 | 0.04013 | 0.03705 | 0.03859 | 50 | 25.91345 |
#2 | 0.03874 | 0.03615 | 0.03744 | 51.3 | 26.7094 |
#3 | 0.03091 | 0.03461 | 0.03276 | 53.6 | 30.52503 |
#4 | 0.03288 | 0.0245 | 0.02869 | 55.5 | 34.85535 |
Puede verse en la Tabla 2 que con el aumento de la dureza, la resistencia al desgaste de las muestras # 1 - # 4 aumenta a su vez. Por tanto, se puede concluir que la pérdida por desgaste de los materiales está directamente relacionada con la dureza de los materiales. Cuanto mayor es la dureza, menor es la pérdida de peso, mejor es la resistencia al desgaste de los materiales. Además, los carburos dispersos en la matriz también contribuyen a la resistencia al desgaste de los materiales, pero el efecto es menor que el de la dureza debido a los pocos carburos precipitados.
Resultados
- Los revestimientos para molinos de bolas de acero de baja aleación estudiados en este documento tienen alta capacidad de endurecimiento y alta estabilidad al revenido.
- Después de templar a 850-930 ℃ y templar a 200-290 ℃, se obtiene martensita de listones finamente templada, lo que hace que el acero tenga alta resistencia, alta tenacidad y alta resistencia al desgaste.
- Cuanto mayor sea la dureza, menor será la pérdida de peso, mejor será la resistencia al desgaste.
Sobre el autor:
Fabricante de revestimientos de molinos de China, Qiming Machinery es líder en el diseño, fabricación y suministro de revestimientos para molinos para las industrias de extracción y procesamiento de minerales. Ofrece a los clientes soluciones completas de revestimiento antidesgaste para molinos que aumentan el rendimiento, la disponibilidad del equipo y reducen los costos de mantenimiento. Sus revestimientos de molino también se prueban para resistir el nivel de acidez de diferentes elementos que pueden estar presentes en el proceso de molienda. Una vida de fresado más larga para su máquina significa menos gastos y más ganancias o ingresos para su empresa.