Навіщо досліджувати молотки з легованої сталі?
Молоткові млини широко використовуються в гірничодобувній промисловості, металургії, електроенергетиці, будівельних матеріалах, хімічній промисловості та інших галузях для подрібнення різних видів сировини. Молоток є основною шліфувальною частиною машини, і вона має велику швидкість та інерційну силу в робочих умовах. Отже, матеріал, необхідний для виготовлення молотка, повинен не тільки мати достатню ударну стійкість для запобігання поломки, але також повинен мати чудову зносостійкість.
В даний час більшість молотків, що використовуються в Китаї, - це молотки малого та середнього розміру, як правило, важать близько 10 кг, а більші - від 50 до 90 кг, а матеріалом є в основному високомарганцева сталь. Після обробки водою, що зміцнює воду, високомарганцева сталь має аустенітну структуру з дуже високою в'язкістю, що є матеріалом з низькою твердістю та високою в'язкістю. Однак в умовах слабкого удару ефект загартовування роботи поганий, а термін служби короткий. У розвинених країнах, таких як Європа та США, великі молоткові млини використовуються для дроблення скрапованих автомобілів. Вага подрібнювача становить близько 200-500 кг. Як правило, із збільшенням розміру великих деталей загартовування важче гарантувати, тим важче контролювати рівномірність твердості, а ударна в'язкість значно зменшиться. Тому вибір матеріалу та контроль процесу його виробництва будуть більш суворими у виробництві цього надвеликого молотка.
Для того, щоб лити ці великі молоткові млини або подрібнювачі, компанія Qiming Casting дослідила молотки із легованої сталі, які, очевидно, покращують термін експлуатації.
Експеримент із виготовлення молотків із легованої сталі вагою 250 кг
Аналіз матеріалів
Конструкція складу сплаву повинна повністю враховувати відповідність вимогам до експлуатаційних характеристик сплаву. Принцип конструкції полягає у забезпеченні достатньої загартовуваності та високої твердості та в'язкості.
- Вуглецевий елемент. Вуглець є ключовим елементом, який впливає на мікроструктуру та експлуатаційні характеристики низько- та середньолегованих зносостійких сталей. Різна кількість вуглецю може отримати різні співвідношення між твердістю та в'язкістю. Низьковуглецеві сплави мають вищу в'язкість і низьку твердість, а високовуглецеві сплави мають високу твердість і недостатню в'язкість. Вуглецеві сплави мають вищу твердість і хорошу в'язкість. Для того, щоб отримати більш високу в'язкість, щоб відповідати умовам використання важких і великих зносостійких деталей з більшою ударною силою, діапазон вуглецевих елементів вибирається від 0.2 до 0.3%.
- Кремнієвий елемент. Кремній головним чином відіграє роль у зміцненні твердих розчинів у сталі, але занадто високий вміст Si збільшує крихкість сталі, тому його вміст становить від 0.2 до 0.4%.
- Марганцевий елемент. З одного боку, марганець у сталі відіграє роль у зміцненні твердого розчину, покращуючи міцність і твердість сталі, а з іншого боку, покращуючи загартовуваність сталі, але занадто високий марганець збільшить кількість затриманого аустеніту, тому Вміст марганцю визначається як 1.0 - 2.0%.
- Хром елемент. Cr відіграє провідну роль у низьколегованій зносостійкій литій сталі. Cr може бути частково розчинений в аустеніті для зміцнення матриці без зменшення в'язкості, затримки перетворення аустеніту та збільшення загартовуваності сталі. Розумне поєднання хрому, марганцю та кремнію може значно покращити загартовуваність. Cr має більший опір відпуску і може зробити рівномірним показники товстого торця. Тож його вміст становить 1.5 - 2.0%.
- Елемент молібден. Молібден у сталі може ефективно вдосконалити литу структуру, поліпшити рівномірність секції, запобігти появі крихкості відпуску, поліпшити стабільність відпуску сталі, покращити ударну в'язкість, значно збільшити загартовуваність сталі та збільшити міцність сталі, тому вміст від 0.1 до 0.3%.
- Нікелевий елемент. Нікель - головний легуючий елемент, який утворює та стабілізує аустеніт. Додавання певної кількості Ni може поліпшити загартовуваність і змусити структуру зберігати невелику кількість затриманого аустеніту при кімнатній температурі для поліпшення його в'язкості. Вміст від 0.1 до 0.3%.
- Мідний елемент. Мідь не утворює карбідів і існує в матриці у твердому розчині, що може поліпшити в'язкість сталі. Крім того, Cu також має функцію, подібну до Ni, яка може покращити загартовуваність і електродний потенціал підкладки, а також підвищити корозійну стійкість сталі. Це особливо важливо для зносостійких деталей, які працюють в умовах вологого помелу. Додавання Cu в леговану сталь становить 0.8-1.00%.
- Розсіяні елементи. Додавання мікроелементів до низьколегованої зносостійкої сталі є одним із найефективніших способів поліпшення її експлуатаційних характеристик. Він може вдосконалити структуру лиття, очистити межі зерен, покращити морфологію та розподіл карбідів та включень, а також зробити низьколеговану зносостійку сталь, що підтримує достатню в'язкість.
- Сірка та фосфорний елемент. Сірка і фосфор є шкідливими елементами, які легко утворюють в сталі граничні включення зерна, підвищують крихкість сталі та підвищують тенденцію до розтріскування виливків під час лиття та термічної обробки. Отже, як P, так і S повинні бути менше 0.04%.
Отже, легована сталь забиває хімічний склад за наступною таблицею:
Хімічний склад молотків із легованої сталі (%) | ||||||||||
Елемент | C | Si | Mn | Cr | Mo | Ni | Cu | V, Re | P | S |
зміст | 0.2-0.3 | 0.2-0.4 | 1.0-2.0 | 1.5-2.0 | 0.1-0.3 | 0.1-0.3 | 0.8-1.0 | простежувати | <0.04 | <0.04 |
Процес виробництва
Процес виготовлення молотків із легованої сталі вагою 250 кг включає процес плавлення, процес лиття, процес термообробки та випробування на продуктивність.
Процес плавлення
Леговану сталь виплавляли в індукційній печі з середньочастотною частотою 1 т, а сплави готували із сировиною, такою як металобрухт, чавун, низьковуглецевий ферохром, феромарганець, феромолібден, електролітичний нікель та рідкісноземельні сплави. Після плавлення відбирають зразки для хімічного аналізу перед піччю і додають сплави за результатами аналізу. Коли склад і температура досягають вимог до печі, алюміній вставляється і розкислюється; під час процесу різання для модифікації додають рідкісноземельні Ti і V.
Процес лиття
У процесі формування застосовується лиття з піску. Після того, як розплавлена сталь вийде з печі, дайте їй нерухомо стояти в ковші, а коли температура опуститься до 1450 градусів Цельсія, починайте заливку. Для того, щоб розплавлена сталь швидко заповнювала піщану форму, слід використовувати більшу ворота (на 20% більшу, ніж у звичайної вуглецевої сталі). Застосовується послідовний метод затвердіння із холодним залізом, суміщеним із стояком, і зовнішній нагрівальний метод для стояка для покращення часу подачі та здатності живлення стояка для отримання щільної литої структури. Розмір розливного молота із легованої сталі становить 700 мм х 400 мм х 120 мм, а вага цільної деталі - 250 кг. Після того, як виливка очищена, її відпалюють при високій температурі, а потім ріжучий стояк вирізають.
Термічна обробка
Застосовується процес термообробки загартування + відпустка, і з метою запобігання гартувальним тріщинам у монтажних отворах застосовується часткове загартування. Для нагрівання виливків використовується піч коробчастого типу, температура аустенізації становить (900 ± 10) градусів Цельсія, а збереження тепла - 5 год. За допомогою спеціальної рідини для гасіння водяного скла швидкість охолодження знаходиться між водою та маслом. Це дуже корисно для запобігання гартувальних тріщин і деформацій, що гартують, і це гартувальне середовище має низьку вартість, безпеку та практичність. Після гартування застосовується низькотемпературний процес відпуску, температура відпуску становить (230 ± 10) градусів Цельсія, а збереження тепла - 6 год.
Тест на продуктивність
- Вимірювання в'язкості. Відповідно до положень національного стандарту GB / T 22951994, ударна проба має стандартний U-виріз Шарпі. Виміряйте енергію удару зразка зразка на машині для випробування ударної в'язкості маятника JB5 та виміряйте розмір ударного руйнування зразка мікрометром.
- Вимірювання твердості. Вимірювач твердості HR6150D Rockwell використовується для вимірювання твердості по Роквеллу відповідно до національного стандарту GB / T 23071991. Для тестування твердості зразка, значення твердості взятого зразка 10 мм * 10 мм * 120 мм за EDM вимірюється з інтервалом 10 мм від одного кінця до іншого по напрямку довжини.
- Вимірювання розтягування. Відповідно до національного стандарту GB / T 22881987 «Випробування металу на розтяг», використовується машина для випробування на розтяг 5 т, довжина калібру становить 30 мм, а звичайна стандартна швидкість на розтяг - 0.1 мм / с.
Результати експерименту та аналіз
1. Крива TTT з легованої сталі
Крива TTT з легованої сталі - це наступне зображення:
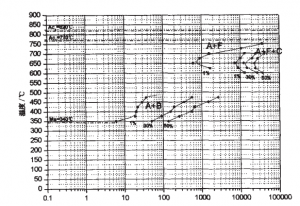
Крива TTT з легованої сталі
З кривої TTT:
- Між кривими перетворення високотемпературного фериту, перліту та середньотемпературного бейніту є чітка зона затоки. Крива С, що спричиняє перетворення перліту, і крива С перетворення бейніту відокремлюються одна від одної, показуючи появу незалежних кривих С, що належать до типу двох «носів», а область бейнітів ближче до кривої S . Оскільки ця сталь містить карбідоутворюючі елементи Cr, Mo та ін., Ці елементи при нагріванні розчиняються в аустеніті, що може затримати розкладання переохолодженого аустеніту та зменшити швидкість розкладання. Водночас вони також впливають на температуру розкладання недостатньо охолодженого аустеніту. Cr, Mo та ін. Змушують зону перетворення перлітів переходити до більш високої температури та знижувати температуру перетворення бейніту. Таким чином, крива перетворення перліту та бейніту знаходиться в кривій ТТТ. Відокремлення, в середній частині знаходиться переохолоджена метастабільна зона аустеніту, яка знаходиться між 500 ℃ і 600 ℃.
- Температура кінчика носа цієї сталі становить близько 650 ℃, зона перетворення фериту становить 625 ℃ -750 ℃, зона перетворення перліту становить 600 ℃ -700 ℃, а зона перетворення бейніту становить 350 ℃ -500 ℃.
- На кінчику носа при 650 ℃ у високотемпературній перехідній зоні ранній час опадів фериту становить 612 с, найкоротший інкубаційний період перліту - 7 270 с, а при 22 860 с кількість трансформації перліту досягає 50 %; у 400 с інкубаційний період для перетворення в бейніт становить близько 20 с; при 340 ° С відбувається перетворення мартенситу. Видно, що ця сталь має гарну загартовуваність.
2. Механічні властивості
Зразки беруть із корпусу молотків із легованої сталі, випробуваного виробництва, а зразок довжиною 10 мм * 10 мм * 120 мм вирізають ззовні лінійним різанням, а твердість вимірюють від поверхні до центру. Зразки 1 # і 2 # відбираються з частини корпусу молотка, а 3 # зразки відбираються у кріпильному отворі. Результати вимірювання твердості наведені в таблиці.
Твердість молотків із легованої сталі | |||||||
Зразок | Відстань від поверхні / мм | середній | Загальна середня | ||||
5 | 15 | 25 | 35 | 45 | |||
1# | 52 | 54.5 | 54.3 | 50 | 52 | 52.6 | 48.5 |
2# | 54 | 48.2 | 47.3 | 48.5 | 46.2 | 48.8 | |
3# | 46 | 43.5 | 43.5 | 44.4 | 42.5 | 44 |
З таблиці твердості ми можемо знати:
Твердість HRC частини корпусу молотка (1 #) перевищує 48.8, тоді як твердість частини кріпильного отвору (3 #) порівняно нижча. Корпус молотка - основна робоча частина. Висока твердість корпусу молотка може забезпечити високу зносостійкість; низька твердість монтажного отвору може забезпечити високу в'язкість. Це задовольняє різним вимогам до продуктивності різних деталей. Якщо розглянути один зразок, можна виявити, що твердість поверхні, як правило, вища, ніж твердість серцевини, а діапазон коливань твердості не дуже великий.
Механічні властивості молотків із легованої сталі | |||
пункт | 1# | 2# | 3# |
Ударна в'язкість / Дж * см² | 40.13 | 46.9 | 58.58 |
Міцність на розрив / МПа | 1548 | 1369 | 1350 |
Подовження% | 8 | 6.67 | 7 |
% Усадки | 3.88 | 15 | 7.09 |
Дані ударної в'язкості, міцності на розрив та подовження зразків наведені у таблиці вище. З таблиці видно, що ударна в'язкість молотка U-образного відсутності зразків Шарпі перевищує 40 Дж / см², а в'язкість кріпильного отвору найвища - 58.58 Дж / см²; подовження перехоплених зразків становить> 6.6%, а міцність на розрив - понад 1360 МПа. Його пластична в'язкість більш відповідає, і вона вища, ніж ударна в'язкість (20-40 Дж / смXNUMX) звичайної низьколегованої сталі. Взагалі кажучи, якщо твердість вища, в'язкість зменшиться. З наведених вище експериментальних результатів видно, що цей закон в основному відповідає.
Тест на знос
Для вивчення зносостійкості цієї легованої сталі було проведено випробування на зношування на динамічній машині для абразивного зносу MLD-10. Зразки ударного зносу цього випробування виготовляються з прямокутних зразків паралелепіпеда 10 мм * 10 мм * 25 мм, і зразки поміщаються в трикорпусну абразивну систему зносу і марганцеві сталеві молотки використовується як порівняльний зразок, всі за однакових умов проводять випробування на зношення.
- Енергія удару становить 0.2 кг / м
- Час удару - 1 година
- Кількість ударів становить 100 разів / хв
- Розмір частинок використовуваного кварцового піску становить 8-10 меш, а витрата - 120 кг / год
Для того, щоб виключити вплив вихідного стану зразка на результати випробування на стирання, попередньо подрібніть зразок за півгодини до випробування, очистіть його ацетоном і зважте після висихання; потім офіційно носити його протягом 1 години, вимити, висушити і зважити; до і після зносу Різниця в якості - це абсолютна величина зносу. Тест на стирання повторювали двічі. Зважте на прецизійних вагах DT-100 і візьміть середнє значення 2 втрати ваги. Результати наведені в таблиці нижче:
Результати випробування на знос | |||||
Зразок елемента | Носіння в перший раз | Носіння вдруге | Середня втрата ваги | Міцність | Коефіцієнт відносного зносу |
Mn13 | 0.48063 | 0.40724 | 0.44394 | 2.25256 | 1.0 |
1# | 0.32879 | 0.24499 | 0.28689 | 3.48566 | 1.55 |
2# | 0.30906 | 0.34610 | 0.32758 | 3.05269 | 1.36 |
3# | 0.46364 | 0.32143 | 0.39254 | 2.54751 | 1.13 |
З таблиці видно, що за однакових умов зносу зносостійкість робочої частини молотків із легованої сталі збільшується більш ніж у 1.55 рази порівняно із звичайними високомарганцевими сталевими молотками.
Високомарганцева сталь широко застосовується при великих ударних навантаженнях. Його відмінна зносостійкість обумовлена його сильним робочим зміцненням та чудовою в'язкістю, обумовленою аустенітною структурою. У цьому випробуванні погана зносостійкість головним чином обумовлена малою енергією випробувального удару та незначним ефектом зміцнення при роботі.
Для сталі порядок впливу структури матриці на зносостійкість такий: ферит, перліт, бейніт та мартенсит поступово зростають. Оскільки мартенсит має найвищу твердість, найвища зносостійкість належить мартенситу і загартованому мартенситу. Але якщо твердість однакова, нижчий бейніт ізотермічного перетворення набагато кращий, ніж загартований мартенсит. Матрична структура зразка 1 # переважно мартенситна, з високою твердістю та хорошою зносостійкістю.
Зносостійкість молотків із легованої сталі, очевидно, різна в різних положеннях. Це пояснюється тим, що коли матеріал піддається абразивному зносу, швидкість зносу складається з двох частин, одна - знос, спричинений механізмом різання, і це головним чином залежить від твердості матеріалу; Однією частиною є знос, спричинений механізмом втоми, що відображає в'язкість матеріалу. Тому ударний знос пов'язаний з твердістю і в'язкістю матеріалу. Зразок 3 # має найвищу в'язкість, але його твердість значно знижується, що знижує зносостійкість. Зразок 1 # має найкращу твердість, середню в'язкість, найкращі комплексні показники та найкращу зносостійкість. Коротше кажучи, за умови ударного абразивного зносу, щоб отримати високу зносостійкість сталі, вона повинна мати гарне поєднання високої твердості та високої в'язкості.
Молотки із легованої сталі методом лиття Цимін
Qiming Casting - це ваша ливарня для подрібнювачів та дробарок! Всі запасні деталі для лиття Qiming забезпечені системою контролю якості ISO9001: 2015 і поставляються лише після дотримання наших суворих стандартів якості. Ми прагнемо задовольнити ваші потреби у запасних частинах професійно та ефективно. Наш відділ підтримки клієнтів готовий допомогти вам із формулюванням ціни, перевірити інвентар або просто відповісти на технічне питання. Поговоріть зі своїм фахівцем з кастингу Qiming сьогодні про ваші конкретні потреби!
[wpforms id = ”3777 ″]