90кг марганецті болат балғасын зерттеу және қолдану
Жылдар бойы құрылыс материалдары, металлургия, тау-кен өнеркәсібі, электр энергетикасында ірі балғалар ұсақтағыш балғалары қарапайымдан жасалған марганецті болат, балғаның салмағы 70 кг-нан аз. Қолдануда оның тозуға төзімділігі төмен және оны бұзуға оңай, бұл жабдықты кейде оқыс зақымдайды. Қытайдың заманауи индустриясының қарқынды дамуымен тәуліктік өнімі 2000-4000 тонна цемент өндіретін желілер бірінен соң бірі іске қосылды. 1980 жылдардың аяғында Қытай Германиядан, Даниядан және басқа елдерден ірі балға ұнтақтағыштарын дәйекті түрде әкелді. Қытайда табысты өндіріс тәжірибесінің болмауына байланысты тірек қуаты 90 кг-нан асатын балғаларды шетелден әкелуге тура келеді.
90 кг-нан астам балғамен ауыр салмақпен, жоғары жылдамдықты циклдік соққы күшімен жабдықталған үлкен балға ұсатқыш, жұмыс жағдайы өте нашар, ал қарапайым жоғары марганецті болат сынықтарды да, тозуға да төзімділікті қамтамасыз ете алмайды. Бұл жағдайда біз Джидун, Чжуцзян және басқа да цемент зауыттары Германия мен Даниядан әкелінген балғаларды зерттедік және Қытайдың ресурстарының сипаттамаларымен біріктіріп, 90 кг маркалы супер жоғары марганецті болат балғасын жасадық.
Марганецті болат балға химиялық құрамы
90 кг салмақтағы марганецті болат балғасының жұмыс жағдайына сүйене отырып, балға соққыға төзімділігі жоғары, тозуға төзімділігі және сынуға төзімді болуы керек. Сонымен бірге, өз салмағы мен қиманың үлкен қалыңдығына сәйкес келесі композициялық жобалау жүзеге асырылады.
- Көміртек (С): көміртек - бұл болаттағы әр түрлі қасиеттерге әсер ететін басым элемент. Болатты жоғары беріктікке, қаттылыққа, тозуға төзімділікке және сынуға жол бермейтін жеткілікті беріктікке ие ету үшін w (c) = 0.95% ~ 1.25%.
- Марганец (Mn): марганецтің көміртегі қатынасы суды қатайтып тазалағаннан кейін аустенит құрылымын алу болып табылады. Марганецті W (MN) = 13% негізінде ұдайы көбейткенде, болаттың беріктігі мен беріктігі онша жақсармаса да, қалың және үлкен қиманың құрылымында карбидтердің жауын-шашын мөлшері азаяды, бұл үлкен қаттылықты жақсартуға әсер етеді. Демек, бір уақытта болатқа хромның тиісті мөлшерін қосып, марганец құрамының жоғарылауы хромның құйылған күйде карбидті жауын-шашынның пайда болуына зиянды әсерін төмендетуі мүмкін. Сондықтан болаттағы марганец мөлшері 17% ~ 20% дейін көбейтіледі.
- Кремний (Si): Кремний - бұл әдеттегі мазмұн, ол қатты ерітіндіні күшейту әсеріне ие. 0.40% ~ 0.80% кремний қосу - бұл тотықсыздандыру және құю процесінің өнімділігін жақсарту. Егер кремнийдің құрамы одан әрі жоғарыласа, болаттың беріктігі нашарлайды.
- Хром (Cr): 2.0% ~ 3.0% хром қосу болаттың беріктілігі мен тозуға төзімділігін жақсарту болып табылады. Егер хром мөлшері тым көп болса, болаттың беріктігі төмендейді және қасиеттері нашарлайды.
- Молибден (Mo): болатта аз мөлшерде карбидтің болуы тозуға төзімділікті және беріктік беріктігін жақсарту үшін пайдалы. 0.20% ~ 0.50% молибденді қосудың мақсаты - болаттағы карбидтің таралуы мен морфологиясын жақсарту және болаттың микроқұрылымы мен қасиеттерін жақсарту.
- Фосфор және күкірт (P, S): болаттағы зиянды элементтер, материалдардың механикалық қасиеттерін төмендетеді, құю және термиялық өңдеу кезінде құймалардың крекинг тенденциясын жоғарылатады және болатқа үлкен зиян келтіреді. Сондықтан w (P) ≤ 0.07%, w (s) ≤ 0.05% қатаң бақылануы керек.
Сондықтан бұл балғалардың химиялық құрамы келесідей:
- C 0.95% ~ 1.25%
- Mn 17% ~ 20%
- Cr 2% ~ 3%
- Mo 0.2% ~ 0.5%
- Si 0.4% ~ 0.8%
- P ≤ 0.07%
- S ≤ 0.05%
Термиялық өңдеу процесінің механикалық қасиеттері мен микроқұрылымына әсері
Кесте 2 Термиялық өңдеу процесінің сынақ нәтижелері | ||||||
Сөндіру температурасы | 1 ℃ | 1100 ℃ | 1150 ℃ | |||
Үлгі мәні | Орташа мән | Үлгі мәні | Орташа мән | Үлгі мәні | Орташа мән | |
Беріктік шегі | 640 | 679 | 851 | 813 | 648 | 726 |
772 | 832 | 865 | ||||
625 | 755 | 665 | ||||
Әсер ету қаттылығы | 39 | 65 | 166 | 176 | 122 | 116 |
46 | 175 | 93 | ||||
110 | 187 | 132 | ||||
Қаттылық (HB) | 241 | 240 | 240 | 238 | 213 | 210 |
252 | 245 | 211 | ||||
227 | 230 | 205 | ||||
Металлографиялық құрылым | Остенит + карбид (4а дәрежесі) | Остенит + карбид (4а-3а дәрежесі) | Остенит + карбид (3а дәрежесі) | Остенит + карбид (3а дәрежесі) | Остенит + карбид (3а дәрежесі) | Остенит + карбид (4а-3а дәрежесі) |
Остенит + карбид (4а дәрежесі) | Остенит + карбид (3а дәрежесі) | Остенит + карбид (4а дәрежесі) | ||||
Остенит + карбид (3а дәрежесі) | Остенит + карбид (3а дәрежесі) | Остенит + карбид (4а дәрежесі) |
Біз салыстыру үшін үш түрлі термиялық өңдеу температураларына эксперименталды үлгілердің үш тобын жасадық:
- Марганецті болат балғасының карбиді 1050 ℃ суды қатайтқаннан кейін аустенитке аз ериді, нәтижесінде қаттылығы жоғары, соққыға төзімділігі төмен және беріктік күші жетеді, бұл жеткіліксіздіктің және беріктігінің жеткіліксіздігі салдарынан балғаның сынуына әкеледі;
- 1150 ℃ суды қатайтып өңдеуден кейін аустенитке ерітілген карбидтердің мөлшері сөндіру температурасының жоғарылығына байланысты болады, нәтижесінде қаттылығы төмен, бұл тозуға төзімділікті азайтады және қызмет ету мерзімін қысқартады;
- 1100 Ом-да өңделген марганец болатының беріктігі мен соққыға төзімділігі басқа екі топқа қарағанда жақсы, кермектігі мен идеалды микроқұрылымы жоғары. Аустенит матрицасында карбидтердің ақылға қонымды таралуы материалдың тозуға төзімділігін жақсарту үшін пайдалы. Сонымен бірге ол беріктігі мен беріктігін сақтай алады және жақсы жан-жақты механикалық қасиеттерге ие. Бұл балғаның жұмыс жағдайында қауіпсіз жұмыс істеуін қамтамасыз ете алады.
Сынақ нәтижелері бойынша біз суды қатайтып тазартуды жүзеге асыратын 1100 choose таңдаймыз
Марганецті болат балғамен өндіріс процесін басқарудың негізгі нүктелері
90 кг-нан асатын балғалар пайдалану кезінде қауіпсіз және сенімді болуы керек және тозуға төзімділігі жақсы болуы керек, сондықтан өндіріс процесі қатаң бақылануы керек.
Ериді
Бұл материал электр доғалық пешке және орташа жиіліктегі индукциялық пешті балқытуға жарамды, химиялық құрамы қатаң бақылануы керек, әсіресе P, s мөлшері стандарттан аспауы керек. Сынықтар таза және тотсыз болуы керек. Пештің қорытпасы мен қорытпасын кейінгі кезеңде 400 ℃ жоғары пісіру керек. Суық иілу сынағы соққыға дейін жүргізілуі керек. Қақтау температурасы 1 460 ~ 1 500 at деңгейінде қатаң бақылануы керек.
Кастинг
Құю процесі тік құю болып табылады, ал қалыптың беті алкоголь негізіндегі тез құрғатылатын магний оксидімен жабылған. Дәнді тазарту және беттің сапасын жақсарту үшін құю температурасын 1 430 ℃ мен 1 460 ℃ аралығында қатаң бақылау керек.
термоөңдеу
Термиялық өңдеу - бұл материалдың ең жақсы өнімділігін алуға кепілдік, ал өндіріс процесте қатаң түрде жүргізілуі керек (1-суретті қараңыз).
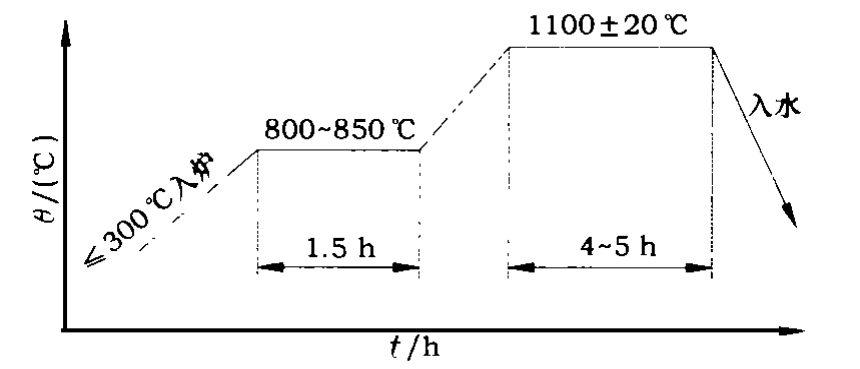
Сурет 1. 90кг марганецті болат балғамен термиялық өңдеу
Тексеру
Марганецті болат балғамен оның жұмысына әсер ететін құю ақаулары болмауы керек, мысалы, шөгу қуысы, шөгілетін кеуектілік, ішкі және сыртқы жарықтар және т.б .. Ультрадыбыстық тексеру фабрикадан шығар алдында бір-бірлеп жүргізілуі керек.
Марганецті болат балғамен Qiming Casting®
Марганецті болат балғалары туралы айтатын болсақ, Qiming Casting балғаш диірменге, ұсақтағышқа және цемент тұтынушыларына арналған тозуға арналған бөлшектерді шығарды. Барлық Qiming Casting ауыстыру бөлшектері ISO9001: 2015 сапаны бақылау жүйесімен қамтамасыз етілген және біздің қатаң сапа стандарттарына сәйкес келгеннен кейін ғана жеткізіледі. Біз сіздің қосалқы бөлшектеріңіздің қажеттіліктерін кәсіби және тиімді түрде қанағаттандыруға дайынбыз. Біздің клиенттерді қолдау бөлімі сізге баға ұсыныстарына, тауарлық-материалдық құндылықтарды тексеруге немесе техникалық сұраққа жай ғана жауап беруге көмектеседі. Бүгін Qiming Casting маманымен нақты қажеттіліктеріңіз туралы сөйлесіңіз!
[wpforms id = ”3777 ″]